What are the different types of electronic adhesives, and what are their distinct characteristics?
What are the different types of electronic adhesives, and what are their distinct characteristics?
With the continuous development of our country’s industry, lightweight, high-strength engineering materials in electronics, chemical, construction, automotive, military, medical, and other fields have wide applications, allowing people to reduce the loss of resources and improve the urgent requirements of the quality of the products. The adhesive has received high attention and has a wide application prospect.
Electronic adhesives are specialized adhesives used in various applications within the electronics industry. They are designed to provide reliable bonding and electrical conductivity while offering specific properties suited to different requirements. Here are some common types of electronic adhesives and their distinct characteristics:
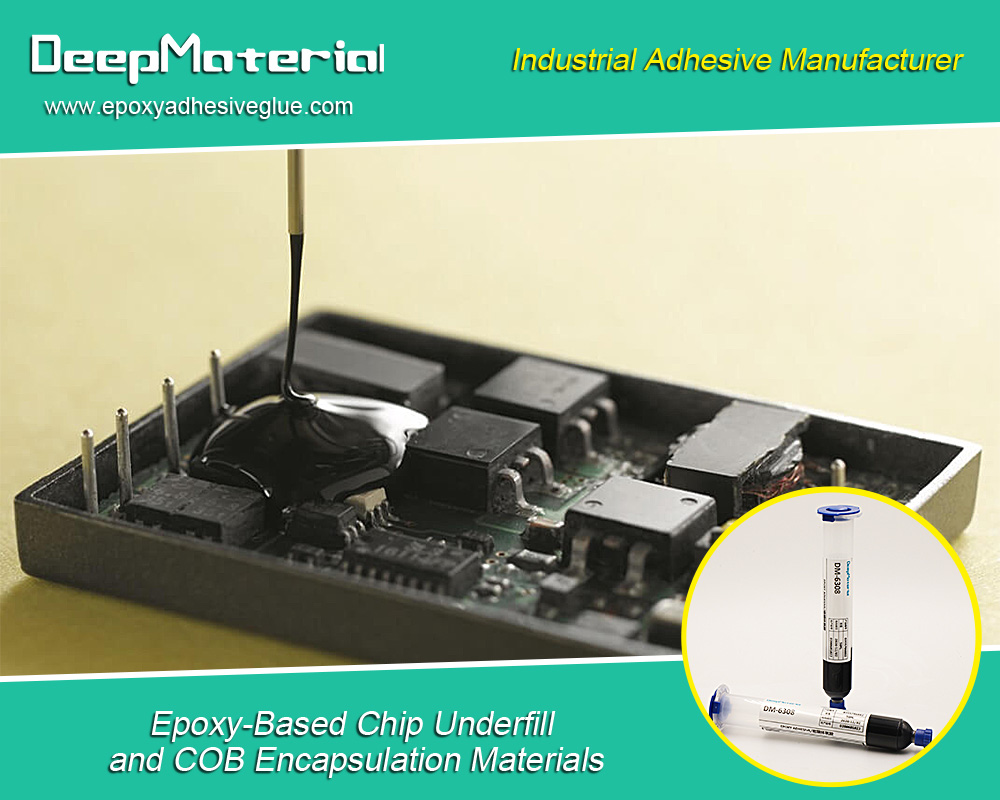
Conductive Adhesives:
Silver-filled: These adhesives are formulated to conduct electricity and provide electrical connections between components. They contain conductive fillers like silver or copper. Conductive adhesives are commonly used for bonding electrical components, attaching surface-mounted devices, and creating electrical paths.
Carbon-filled: Adhesives filled with carbon particles offer electrical conductivity and are often used in applications where silver-filled adhesives are not suitable due to cost or compatibility issues.
Electrically Insulating Adhesives: These adhesives are designed to provide electrical insulation and prevent the flow of electricity. They are used to encapsulate or coat sensitive electronic components to protect them from moisture, dust, and other environmental factors. Electrically insulating adhesives typically have high dielectric strength and low electrical conductivity.
Epoxy Resins: Epoxy-based adhesives provide excellent insulation properties and are widely used for bonding and encapsulation in electronic assemblies.
Silicone-Based: Silicone adhesives are flexible, have high-temperature resistance, and excellent electrical insulation properties. They are often used in applications requiring flexibility or exposure to extreme temperatures.
Thermally Conductive Adhesives: These adhesives are formulated to transfer heat efficiently from heat-generating components to heat sinks or other cooling mechanisms. They contain thermally conductive fillers like ceramics or metal oxides. Thermally conductive adhesives are used in applications where heat dissipation is critical, such as bonding power devices, LED assemblies, and heat sinks.
Silicone-Based: These adhesives are filled with thermally conductive particles, such as ceramics or metal oxides. They provide good heat dissipation and are commonly used for bonding heat sinks, power devices, and other components requiring thermal management.
Epoxy-Based: Epoxy-based adhesives with thermally conductive fillers offer high thermal conductivity and are suitable for applications where high bond strength and thermal transfer are required.
UV Curable Adhesives: These adhesives cure or solidify when exposed to ultraviolet (UV) light. They offer rapid curing times, allowing for faster production cycles. UV curing adhesives are used in applications where quick bonding or sealing is required, such as in electronics assembly, medical devices, and optoelectronics.
UV Curable Epoxy: These adhesives cure rapidly when exposed to UV light, offering fast bonding and high strength. They are commonly used in applications where quick processing or precise positioning is required.
UV Curable Acrylic: UV curable acrylic adhesives provide good adhesion to a wide range of substrates and are often used for display assemblies, glass bonding, and optical applications.
Underfill Adhesives:
Underfill Epoxy: Underfill adhesives are used to fill gaps between electronic components and printed circuit boards (PCBs), providing mechanical reinforcement and improving reliability. Epoxy-based underfills offer high strength and thermal resistance.
Electrically Conductive Films:
Anisotropic Conductive Films (ACF): ACFs are used for bonding flexible circuits to rigid substrates. They contain conductive particles that provide electrical connectivity only in the z-axis, allowing for reliable electrical connections without short circuits.
Optical Adhesives:
These adhesives are transparent or have low refractive index to minimize light scattering and allow optical clarity. They are used for bonding optical components like lenses, displays, and fibers in devices such as cameras, sensors, and fiber optic communication systems. Optical adhesives provide high light transmission and excellent adhesion to various substrates.
Epoxy Adhesives:
Epoxy adhesives provide excellent bond strength, chemical resistance, and durability. They are versatile and used in a wide range of electronic applications, including bonding components, potting, encapsulation, and coating. Epoxy adhesives can be electrically conductive or insulating, depending on the formulation.
Silicone Adhesives:
a type of adhesive or bonding agent that is formulated using silicone polymers. These adhesives are known for their excellent flexibility, high temperature resistance, and resistance to moisture, chemicals, and UV radiation. They are widely used in various industries and applications due to their unique properties. Silicone adhesives have excellent resistance to water and moisture. They can provide a reliable bond even in wet or humid environments, making them commonly used in applications such as sealing gaskets, waterproofing electronic components, or bonding in marine environments. Silicone adhesives have excellent thermal stability and electrical insulation properties.
Acrylic Adhesives:
Acrylic adhesives offer good adhesion to a variety of substrates, including plastics, metals, and glass. They provide fast curing times, high bond strength, and resistance to temperature and humidity. Acrylic adhesives are commonly used in electronics assembly and bonding applications.
Polyurethane Adhesives:
Polyurethane adhesives provide strong bonding and flexibility. They offer good resistance to chemicals and environmental factors. Polyurethane adhesives are used in applications where a combination of flexibility and durability is required.
Hot-Melt Adhesives:
also known as hot glue or hot melt glue, are thermoplastic adhesives that are solid at room temperature but become liquid when heated. They are commonly used in a wide range of applications, including packaging, woodworking, crafts, and product assembly. They offer fast bonding and are used for temporary or low-stress applications in electronics assembly,too. Hot-melt adhesives are sensitive to temperature changes. They can soften and lose their bond strength at elevated temperatures, making them unsuitable for high-temperature applications.

These are just a few examples of the different types of electronic adhesives available. Each type has its own specific characteristics and is suitable for different electronic applications based on factors like electrical conductivity, thermal management requirements, optical properties, and environmental conditions. It’s important to select the appropriate adhesive based on the specific needs of the application. The selection of a specific adhesive depends on factors such as the application requirements, substrate materials, electrical conductivity needs, thermal management, and processing conditions. It’s important to consult adhesive manufacturers or suppliers to determine the most suitable adhesive for a particular electronic application.
For more about choosing what are the different types of electronic adhesives, and what are their distinct characteristics, you can pay a visit to DeepMaterial at https://www.epoxyadhesiveglue.com/category/electronic-adhesives-glue/ for more info.