Understanding High Temperature Epoxy for Plastic: Characteristics and Best Practices
Understanding High Temperature Epoxy for Plastic: Characteristics and Best Practices
Epoxy resins are renowned for their versatility and durability, making them indispensable in various industrial applications. Using the proper epoxy is crucial when dealing with plastics exposed to high temperatures. High Temperature epoxy for plastic stands out due to its ability to maintain structural integrity and performance under thermal stress. This article delves into the unique characteristics of High Temperature epoxy for plastic and outlines best practices for its application.
What Sets High Temperature Epoxy Apart?
High Temperature epoxy for plastic stands out in adhesives due to its advanced properties tailored for extreme conditions. Unlike standard epoxies, which are typically suited for moderate temperatures and typical environments, High Temperature epoxies are engineered to excel under more demanding scenarios. Here’s what sets them apart:
Exceptional Thermal Resistance
- Heat Stability:High Temperature epoxy for plastic is formulated to endure much higher temperatures than conventional epoxies, often capable of withstanding up to 200°C (392°F) or more. It makes it ideal for applications where heat is a significant factor.
- Thermal Cycling: It remains stable and performs reliably through repeated heating and cooling cycles, which prevents degradation over time and ensures longevity.
Enhanced Chemical Resistance
- Protection Against Aggressive Environments: This epoxy provides robust resistance against various chemicals that can cause standard epoxies to fail. It’s precious in environments where exposure to corrosive substances is a concern.
- Long-Term Durability: High Temperature epoxy maintains its integrity and effectiveness over extended periods by resisting chemical attacks, minimizing the risk of deterioration, and ensuring consistent performance.
Superior Bonding Strength
- Adhesion to Plastics: It offers an exceptional bond to various plastic substrates, including those with low surface energy that are typically challenging for regular adhesives. It ensures a reliable connection where other adhesives might struggle.
- Load-Bearing Capability: High Temperature epoxy is capable of supporting significant mechanical loads, even under high temperatures. It ensures that the bonded parts remain securely attached, providing strength and reliability in demanding applications.
Application Best Practices
When working with High Temperature epoxy for plastic, achieving optimal performance hinges on meticulous attention to several critical application practices. Here’s a structured guide to ensure you get the best results:
Surface Preparation
- Clean the Surface: Begin by thoroughly cleaning the plastic surface. It should be free of dust, grease, and any other contaminants. This step is crucial for ensuring strong adhesion of the epoxy.
- Roughen the Surface: Lightly sand or scuff the plastic to enhance the mechanical interlock between the epoxy and the plastic. This process helps the epoxy adhere more effectively.
Mixing and Application
- Instructions: Strictly adhere to the manufacturer’s specified mixing ratios and guidelines. Accurate mixing is essential for achieving the epoxy’s desired thermal and mechanical properties.
- Apply Evenly:Use a brush or applicator to spread the epoxy evenly across the prepared surface. Avoid air bubbles and ensure that the application is uniform to prevent weak spots.
Curing Process
- Control Temperature: Cure the epoxy within the recommended temperature range to ensure it achieves optimal strength and durability. Temperature control is critical for the epoxy’s performance under high temperatures.
- Allow Sufficient Time: Ensure you allow the epoxy to cure fully according to the manufacturer’s instructions. Premature exposure to high temperatures or mechanical stress can compromise the epoxy’s effectiveness.
Adhering to these best practices can maximize the performance and longevity of High Temperature epoxy applied to plastic surfaces.
Troubleshooting Common Issues
When working with High Temperature epoxy for plastic, it’s essential to be aware of common issues that might arise, even with careful application. Here’s a comprehensive guide to troubleshooting and ensuring a successful result.
Adhesion Problems
- Inadequate Surface Preparation: One primary reason for poor adhesion is insufficient surface preparation. To ensure the epoxy bonds effectively, you must clean the plastic surface thoroughly to remove contaminants like dust, grease, or oils. Roughing the surface with sandpaper or a similar abrasive can also significantly enhance the epoxy’s grip.
- Incorrect Mixing Ratios: Proper mixing of the epoxy components is crucial for achieving optimal results. Always adhere strictly to the recommended mixing ratios provided by the manufacturer. Deviations from these ratios can lead to adequate curing and strong bonding.
Curing Issues
- Insufficient Cure Time: High Temperature epoxy requires adequate time to cure and fully achieve its maximum strength. It’s vital to follow the manufacturer’s instructions regarding cure time. Rushing this process or subjecting the epoxy to stress before it is fully cured can compromise the bond.
- Temperature Fluctuations: Maintaining a stable temperature during the curing process is essential. High Temperature epoxies are sensitive to temperature changes; fluctuations can result in incomplete curing or premature bond failure. Ensure that the curing environment remains consistent with the epoxy’s specifications.
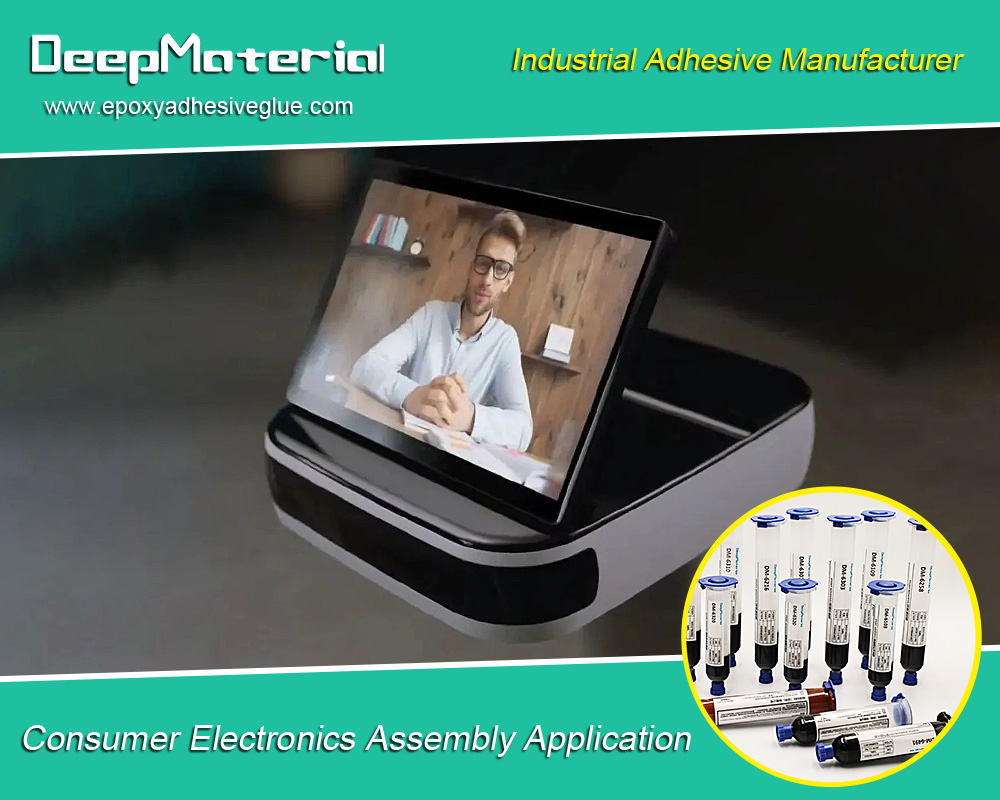
Applications of High Temperature Epoxy for Plastic
High Temperature epoxy for plastic plays a crucial role across several industries due to its exceptional performance under extreme conditions. Its unique properties make it indispensable in various applications where durability and heat resistance are paramount.
Critical Applications of High Temperature Epoxy for Plastic
Automotive Industry:
- Engine Components: This epoxy is essential for bonding and sealing parts exposed to high temperatures in the engine compartment. It ensures that connections remain intact and effective even under intense heat.
- Interior Panels: Interior Panels reinforce and maintain the structural integrity of plastic parts within the vehicle’s interior, which might be subjected to elevated temperatures from engine heat or sun exposure.
Aerospace Sector:
- Thermal Insulation: The epoxy’s thermal resistance is crucial for components that experience drastic temperature fluctuations during flight, ensuring stable and reliable performance.
- Structural Repairs:It is ideal for mending and reinforcing structural parts that face significant thermal stress, extending their longevity and safety.
Electronics and Electrical Applications:
- Heat Shields: High Temperature epoxy attaches heat shields and insulators in electronic devices, safeguarding them from heat-related damage.
- Component Encapsulation: It provides a protective layer around sensitive electronic components, preventing thermal damage and ensuring reliable operation.
These applications highlight the versatility and critical importance of High Temperature epoxy in maintaining the functionality and longevity of components across various sectors.
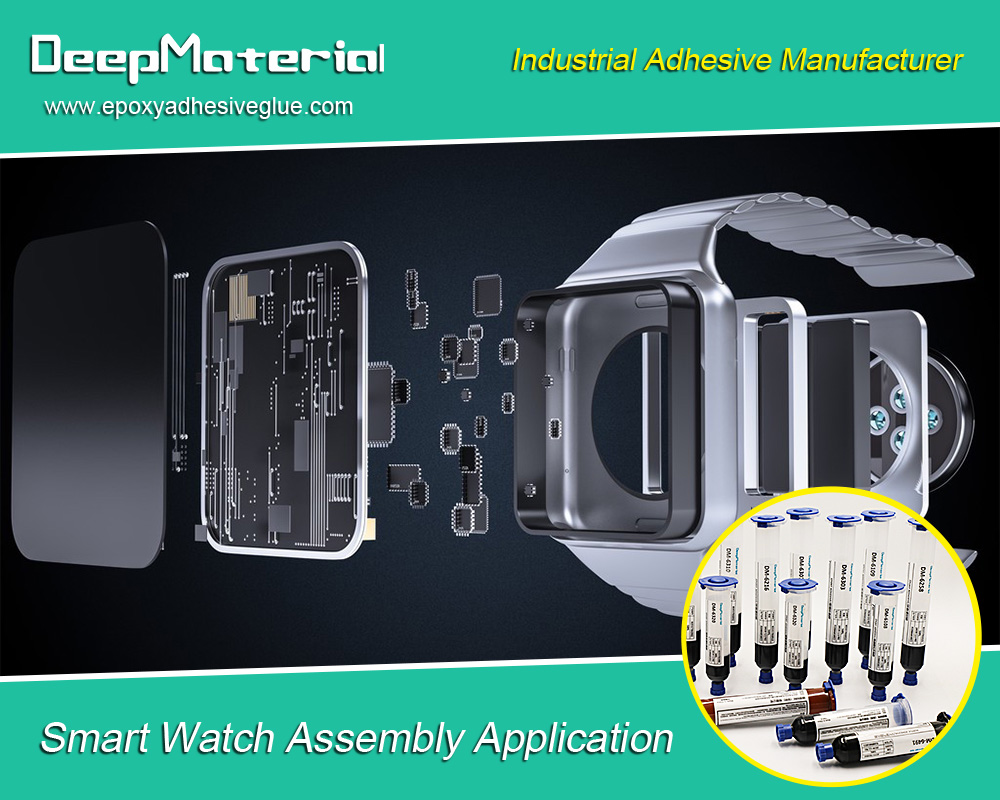
Conclusion
High Temperature epoxy for plastic is a specialized material offering exceptional thermal and chemical resistance, making it indispensable in various high-stress applications. Its unique characteristics, such as superior thermal stability and strong bonding capabilities, make it an ideal choice for challenging environments. By following best practices in application and being mindful of common issues, users can maximize the performance and longevity of their High Temperature epoxy solutions. Understanding these aspects ensures that High Temperature epoxy for plastic meets the demands of its intended applications, providing reliable and durable results.
For more about understanding high temperature epoxy for plastic: characteristics and best practices, you can pay a visit to DeepMaterial at https://www.epoxyadhesiveglue.com/category/epoxy-adhesives-glue/ for more info.