Special Requirements for Epoxy Encapsulated LEDs in Different Application Scenarios
Special Requirements for Epoxy Encapsulated LEDs in Different Application Scenarios
LEDs (Light Emitting Diodes) have been widely used in numerous fields such as lighting, display, automotive electronics, etc., due to their significant advantages of high efficiency, energy conservation, and long lifespan. Epoxy encapsulation LEDs, as a crucial process for protecting LED chips and influencing their performance, has its own unique requirements in different application scenarios. A thorough understanding of these special requirements is of great significance for optimizing the performance of LED products and expanding their application areas.
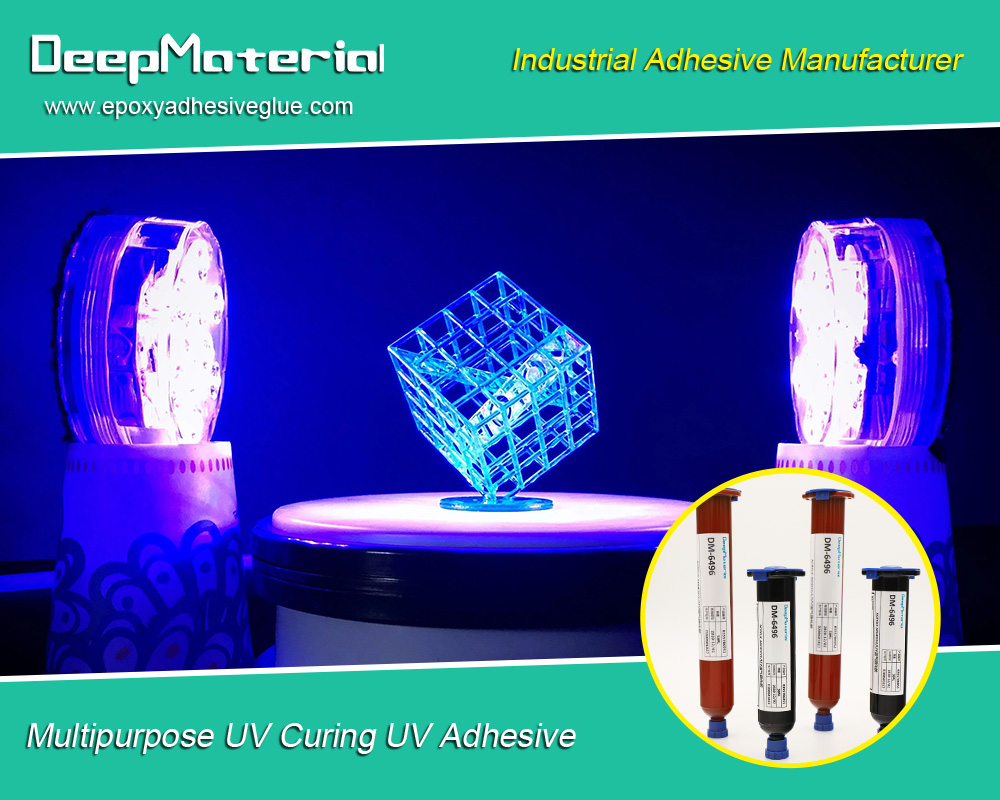
Special Requirements for Epoxy Encapsulated LEDs in the Lighting Field
Optical Properties
- High Transmittance: In lighting applications, to achieve efficient light output, the epoxy encapsulation material needs to have extremely high transmittance. Generally, it is required to have a transmittance of over 90% in the visible light range. High transmittance can reduce the absorption and scattering losses of light in the encapsulation material, allowing as much light as possible emitted by the LED chip to pass through, thus improving the lighting efficiency.
- Good Light Diffusion Property: For some scenarios that require uniform lighting, such as indoor lighting and street lighting, the epoxy encapsulation needs to have good light diffusion performance. By adding appropriate light diffusing agents, the light can be scattered in the encapsulation material, achieving a more uniform light distribution and avoiding the occurrence of light spots and dark areas.
- Color Stability: Lighting products have high requirements for color consistency. The epoxy encapsulation material should have good color stability and not be prone to phenomena such as yellowing during long-term use. Yellowing will cause the color of the light emitted by the LED to shift, affecting the lighting effect and visual experience.
Thermal Properties
- Good Heat Dissipation: LED chips generate a large amount of heat during operation. If the heat cannot be dissipated effectively in a timely manner, the temperature of the chip will rise, which in turn affects its luminous efficiency and lifespan. The epoxy encapsulation material should have a certain thermal conductivity to quickly conduct the heat generated by the chip. At the same time, the design of the encapsulation structure should also take into account the heat dissipation requirements, such as increasing the heat dissipation area.
- Thermal Stability: The epoxy encapsulation material needs to maintain stable performance under different ambient temperatures. It should have a wide operating temperature range, not soften or deform in high-temperature environments, and not crack in low-temperature environments, ensuring that the LED can work normally under various climatic conditions.
Mechanical Properties
- High Hardness and Wear Resistance: In some outdoor lighting and industrial lighting applications, LED lamps may be subject to mechanical collisions and frictions. Therefore, the epoxy encapsulation material needs to have high hardness and wear resistance to protect the LED chip from damage.
- Impact Resistance: During the installation and use of lamps, they may be subjected to a certain degree of impact force. The epoxy encapsulation should have good impact resistance and be able to withstand a certain degree of external impact without cracking, ensuring the reliability of the LED.
Special Requirements for Epoxy Encapsulated LEDs in the Display Field
Optical Properties
- High Color Purity: In display applications, such as LED displays and backlights, the requirements for the color purity of LEDs are extremely high. The epoxy encapsulation material should have an extremely low impurity content to avoid interfering with the color of the light emitted by the LED chip, ensuring that the displayed images are vivid and accurate in color.
- Precise Angle Control: For LED displays, to achieve a good display effect, it is necessary to precisely control the emitting angle of the LEDs. The epoxy encapsulation can adjust the emitting angle of the LEDs through special design and process, enabling the light to propagate in the predetermined direction and improving the viewing angle and contrast ratio of the display.
- Low Light Decay: Display devices usually need to work continuously for a long time, so the requirements for the light decay of LEDs are strict. The epoxy encapsulation material should have good anti-aging performance, effectively suppressing the occurrence of light decay and ensuring that the brightness and color stability of the displayed images remain unchanged during long-term use.
Electrical Properties
- Good Insulation: In display applications, LEDs are usually densely arranged. To avoid electrical short circuits between adjacent LEDs, the epoxy encapsulation material needs to have good insulation performance. It should be able to effectively isolate the electrical connections between different LEDs, ensuring the normal operation of the display device.
- Low Dielectric Constant: With the continuous development of display technology, the operating frequency of LEDs is getting higher and higher. The epoxy encapsulation material with a low dielectric constant can reduce the losses and interferences during signal transmission, improving the performance of the display device.
Dimensional Accuracy
- Tiny Size Encapsulation: In display applications, especially in miniaturized and high-resolution display devices, the requirements for the dimensional accuracy of LEDs are extremely high. The epoxy encapsulation needs to be able to achieve precise encapsulation of tiny sizes to meet the design requirements of the display device.
- Consistency: To ensure the uniformity and consistency of the displayed images, the LEDs of the same batch should have a high degree of consistency in encapsulation size and performance. The epoxy encapsulation process needs to be strictly controlled to ensure that the encapsulation quality of each LED meets the requirements.
Special Requirements for Epoxy Encapsulated LEDs in the Automotive Electronics Field
Environmental Adaptability
- Weather Resistance: Cars are driven outdoors and will be affected by various harsh environmental conditions, such as ultraviolet rays, rainwater, and dust. The epoxy encapsulation material should have good weather resistance, be able to resist the irradiation of ultraviolet rays without aging, discoloration, and other phenomena, and at the same time have water-proof and dust-proof properties to protect the LED chip from the erosion of the external environment.
- High and Low Temperature Resistance: The temperature change range in parts such as the engine compartment of a car is relatively large. The epoxy encapsulation material needs to be able to maintain stable performance in high-temperature (above 150°C) and low-temperature (below -40°C) environments, without deformation, cracking, and other problems, ensuring that the LED can work normally under various temperature conditions.
- Chemical Corrosion Resistance: The interior of a car may come into contact with various chemical substances, such as gasoline, engine oil, and cleaning agents. The epoxy encapsulation material should have good chemical corrosion resistance and be able to resist the erosion of these chemical substances, ensuring the reliability of the LED.
Safety
- Flame Retardancy: Cars are relatively enclosed spaces, and there are high requirements for fire safety. The epoxy encapsulation material should have flame retardant properties, which can prevent the spread of fire in case of a fire and reduce potential safety hazards.
- Vibration and Impact Resistance: Cars will be subject to various vibrations and impacts during driving. The epoxy encapsulation needs to have good vibration and impact resistance, be able to protect the LED chip from damage, and ensure the normal operation of the automotive lighting and display systems.
Optical Properties
- High Brightness and High Contrast: In automotive lighting and display applications, such as headlights, taillights, and instrument panels, LEDs need to have high brightness and high contrast to ensure clear visibility under different lighting conditions. The epoxy encapsulation should be able to optimize the optical performance of the LED and improve its luminous efficiency and brightness.
- Precise Optical Control: For automotive lighting devices such as headlights, it is necessary to precisely control the light distribution of the LEDs to achieve a good lighting effect and avoid glare to other vehicles and pedestrians. The epoxy encapsulation can achieve precise control of the LED light through special optical design and process.
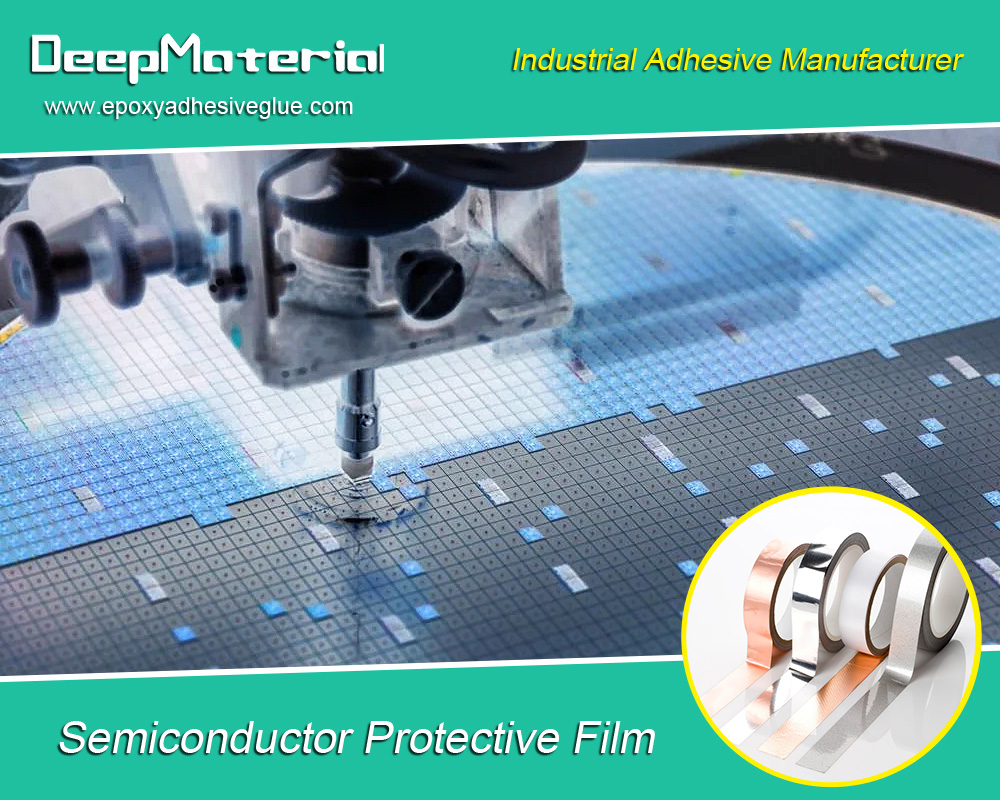
Conclusion
In conclusion, in different application scenarios such as lighting, display, and automotive electronics, there are unique special requirements for epoxy encapsulated LEDs. These requirements cover multiple aspects such as optical, thermal, mechanical, electrical, environmental adaptability, and safety. To meet these requirements, continuous research, development, and improvement of epoxy encapsulation materials and processes are needed to improve the performance and reliability of LED products and meet the needs of different application scenarios. With the continuous progress of science and technology, it is believed that the technology of epoxy encapsulated LEDs will continue to develop and improve, providing higher-quality products and solutions for applications in various fields.
For more about choosing the best special requirements for epoxy encapsulated LEDs in different application scenarios, you can pay a visit to DeepMaterial at https://www.epoxyadhesiveglue.com/category/epoxy-adhesives-glue/ for more info.