Non-Conductive Epoxy Resin Manufacturer: Innovations, Applications, and Market Trends
Non-Conductive Epoxy Resin Manufacturer: Innovations, Applications, and Market Trends
Non-conductive epoxy resins are essential in various industrial applications, particularly in electronics and electrical industries. These resins provide excellent insulation properties, protecting electronic components from electrical interference and mechanical stress. Manufacturing non-conductive epoxy resins involves a complex process that requires precision and a thorough understanding of the chemical properties involved. This article delves into the innovations, applications, and market trends associated with non-conductive epoxy resin manufacturers.
Manufacturing Process of Non-Conductive Epoxy Resins
Raw Materials and Formulation
The production of non-conductive epoxy resins starts with selecting high-quality raw materials. Epoxy resins are typically formed through the reaction of epichlorohydrin and bisphenol-A, creating a thermosetting polymer that exhibits excellent mechanical and adhesive properties. Manufacturers incorporate various fillers and additives such as silica, alumina, or other insulating materials to ensure non-conductivity. The formulation process is critical as it determines the final properties of the epoxy resin, including its thermal stability, mechanical strength, and dielectric properties.
Mixing and Curing
Once the raw materials are selected, they are mixed in precise proportions to achieve the desired properties. The mixing process involves careful control of temperature and pressure to ensure uniform distribution of fillers and additives. After mixing, the epoxy resin undergoes a curing process, where it is heated to initiate a chemical reaction that transforms it from a liquid to a solid state. This curing process can be adjusted to control the final product’s hardness, flexibility, and other mechanical properties. Manufacturers often use advanced techniques such as vacuum degassing to remove any entrapped air, ensuring a defect-free and homogenous resin.
Quality Control
Quality control is a crucial aspect of the manufacturing process for non-conductive epoxy resins. Manufacturers employ various testing methods to ensure the resins meet stringent industry standards. These tests include dielectric strength testing, thermal conductivity measurements, and mechanical property evaluations. Consistent quality control ensures that the resins provide reliable performance in their intended applications, reducing the risk of electrical failures and enhancing the longevity of electronic components.
Applications of Non-Conductive Epoxy Resins
Electronics and Electrical Components
One of the primary applications of non-conductive epoxy resins is in the electronics and electrical industries. These resins are used for encapsulating and potting electronic components, providing insulation and protection from environmental factors such as moisture, dust, and chemicals. They are also used in manufacturing printed circuit boards (PCBs), where they help secure components and provide a stable platform for electronic circuits. The excellent adhesion and thermal stability of non-conductive epoxy resins make them ideal for high-performance electronic devices, including smartphones, computers, and automotive electronics.
Aerospace and Defense
In the aerospace and defense industries, non-conductive epoxy resins play a vital role in ensuring the reliability and performance of critical components. These resins coat and encapsulate sensors, connectors, and other electronic devices in harsh environments. Their ability to withstand extreme temperatures, vibrations, and mechanical stress makes them suitable for use in aircraft, satellites, and military equipment. Additionally, their lightweight nature contributes to aerospace applications’ overall efficiency and performance.
Automotive Industry
The automotive industry also benefits from the use of non-conductive epoxy resins. These resins are used in various applications, including the encapsulation of sensors and control units, bonding lightweight materials, and insulating high-voltage components in electric vehicles. The durability and thermal stability of non-conductive epoxy resins ensure the reliable operation of automotive electronics, contributing to the safety and performance of modern cars. As the automotive industry continues to evolve towards electric and autonomous vehicles, the demand for high-performance non-conductive epoxy resins is expected to grow significantly.
Renewable Energy
The renewable energy sector, including wind and solar power, relies on non-conductive epoxy resins for various applications. In wind turbines, these resins protect and insulate electrical components, ensuring efficient energy generation and transmission. In solar panels, non-conductive epoxy resins encapsulate photovoltaic cells, providing protection from environmental factors and enhancing the panels’ durability. The increasing adoption of renewable energy technologies is driving the demand for non-conductive epoxy resins, highlighting their importance in the transition to sustainable energy sources.
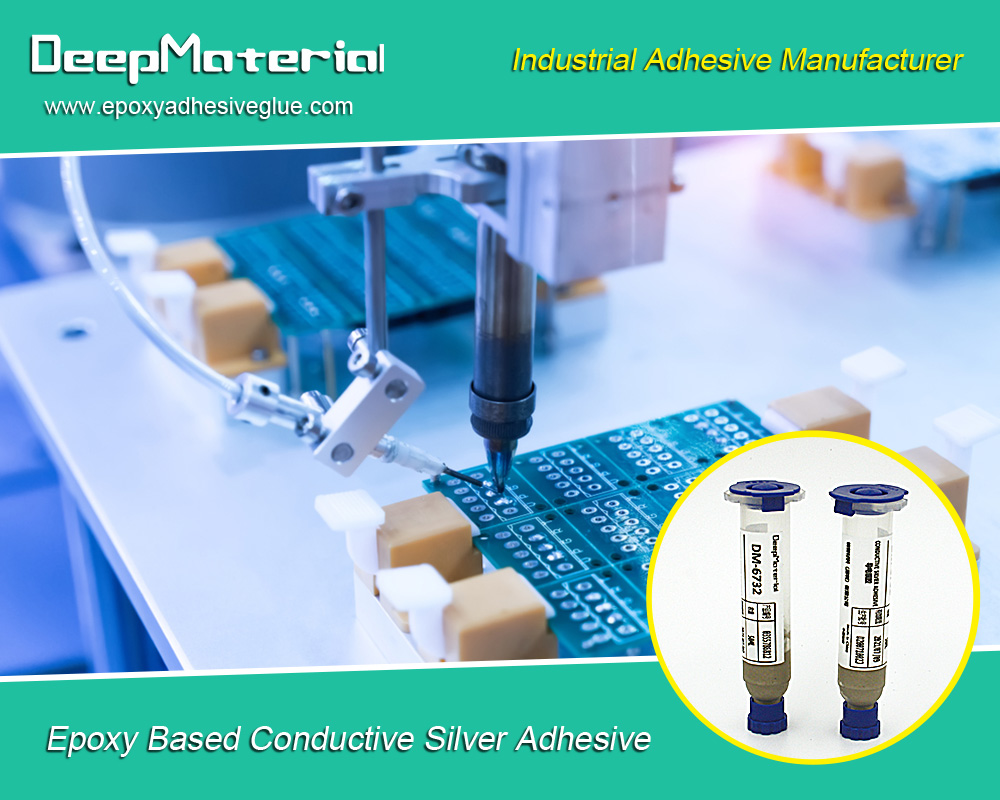
Innovations in Non-Conductive Epoxy Resins
Advanced Formulations
Innovations in the formulation of non-conductive epoxy resins are continuously being developed to enhance their properties and performance. Researchers are exploring using novel fillers and additives to improve these resins’ thermal conductivity, mechanical strength, and dielectric properties. For example, the incorporation of nanomaterials such as carbon nanotubes and graphene can significantly enhance the mechanical and thermal properties of non-conductive epoxy resins, making them suitable for more demanding applications.
Sustainable and Eco-Friendly Resins
With the growing emphasis on sustainability, manufacturers are developing eco-friendly non-conductive epoxy resins. These resins are formulated using bio-based raw materials, reducing their environmental impact and dependence on fossil fuels. Additionally, advancements in recycling technologies enable the recovery and reuse of epoxy resins from end-of-life products, contributing to a circular economy. Sustainable non-conductive epoxy resins are gaining traction in various industries, aligning with global efforts to reduce carbon footprints and promote green manufacturing practices.
Enhanced Curing Techniques
Innovations in curing techniques are also driving advancements in non-conductive epoxy resin manufacturing. Traditional thermal curing methods are being complemented by advanced techniques such as ultraviolet (UV) curing and microwave curing. These techniques offer faster curing times, improved energy efficiency, and better control over the process. UV curing, for example, allows for rapid curing at room temperature, reducing energy consumption and production time. Such advancements in curing technologies are enhancing the overall efficiency and performance of non-conductive epoxy resins.
Market Trends and Future Outlook
Growing Demand in Electronics and Electrical Industries
The increasing demand for electronic devices and technological advancements are driving the growth of the non-conductive epoxy resin market. The proliferation of smartphones, wearable devices, and smart home appliances is creating a significant demand for high-performance epoxy resins that provide reliable insulation and protection for electronic components. Additionally, the trend towards miniaturization and higher circuit densities in electronic devices further fuel the demand for non-conductive epoxy resins with superior dielectric properties.
Expansion in Automotive and Aerospace Sectors
The automotive and aerospace industries are witnessing rapid growth, driven by the adoption of electric vehicles and advancements in aerospace technologies. Non-conductive epoxy resins play a crucial role in these industries by providing various components’ insulation, protection, and bonding solutions. The shift towards electric and autonomous vehicles is expected to drive the demand for non-conductive epoxy resins, particularly for high-voltage applications. Similarly, the aerospace industry’s focus on lightweight materials and advanced electronics contributes to the increasing demand for these resins.
Emphasis on Sustainability and Eco-Friendly Products
The global push towards sustainability is influencing the non-conductive epoxy resin market. Manufacturers are increasingly focusing on developing eco-friendly formulations and adopting sustainable manufacturing practices. The use of bio-based raw materials, recyclable resins, and energy-efficient curing techniques is becoming more prevalent. As industries across the board prioritize environmental responsibility, the demand for sustainable, non-conductive epoxy resins is expected to rise, driving innovation and growth in the market.
Technological Advancements and New Applications
Continuous technological advancements are opening up new applications for non-conductive epoxy resins. Developing next-generation electronic devices, renewable energy technologies, and advanced aerospace systems creates opportunities for innovative resin formulations. Additionally, emerging trends such as the Internet of Things (IoT), 5G technology, and intelligent manufacturing are driving the demand for high-performance, non-conductive epoxy resins that can meet the evolving requirements of these applications.
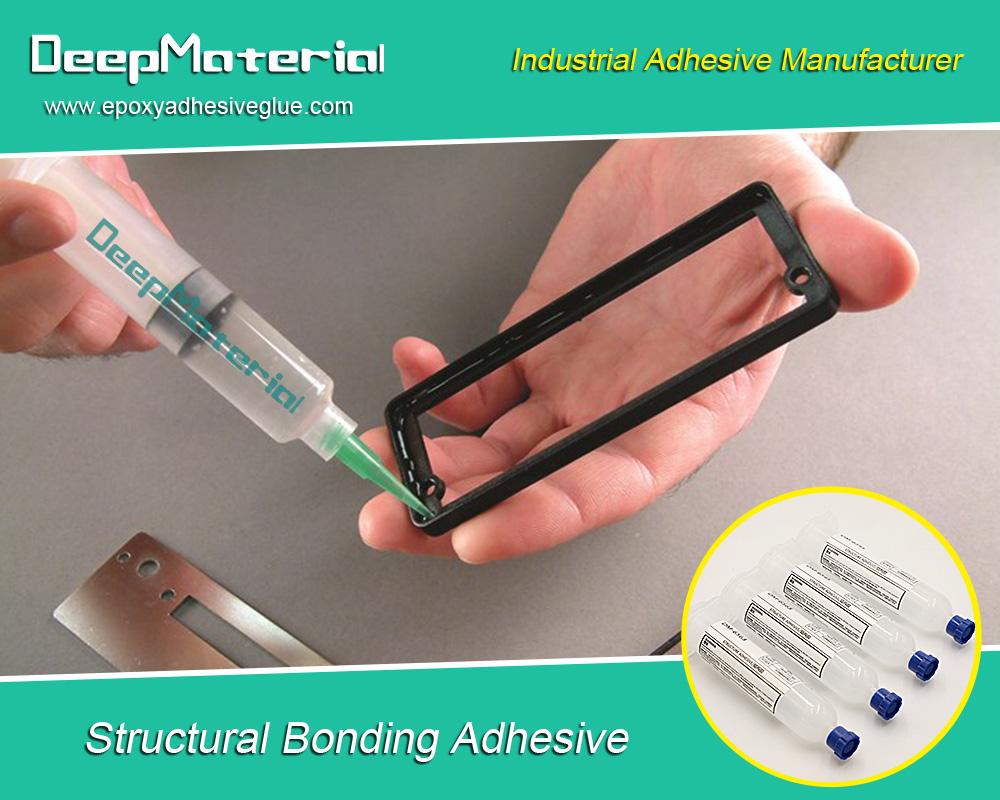
Conclusion
Non-conductive epoxy resins are:
- Indispensable materials in various industries.
- Providing essential insulation.
- Protection.
- Bonding solutions for electronic and electrical components.
The manufacturing process of these resins involves advanced formulation, mixing, and curing techniques to achieve the desired properties. Innovations in raw materials, sustainable formulations, and curing methods are driving the evolution of non-conductive epoxy resins, enhancing their performance and expanding their applications.
The growing demand in the electronics, automotive, aerospace, and renewable energy sectors is propelling the market for non-conductive epoxy resins. As industries prioritize sustainability and adopt new technologies, the future of non-conductive epoxy resins looks promising, with continuous advancements and new opportunities on the horizon. Manufacturers are poised to play a critical role in meeting the evolving needs of these industries, contributing to the advancement of technology and the transition towards a more sustainable future.
For more about choosing the best Non-Conductive Epoxy Resin Manufacturer: Innovations, Applications, and Market Trends
, you can pay a visit to DeepMaterial at https://www.epoxyadhesiveglue.com/category/epoxy-adhesives-glue/ for more info.