How Industrial Bonding Adhesives Improve Product Performance and Durability
How Industrial Bonding Adhesives Improve Product Performance and Durability
Industrial bonding adhesives are a type of adhesive used in product manufacturing to bond two or more substrates together. These adhesives are designed to provide a strong and durable bond that can withstand various environmental conditions and stresses. Industrial bonding adhesives are used in a wide range of industries, including automotive, aerospace, electronics, and construction.
The importance of industrial bonding adhesives in product manufacturing cannot be overstated. These adhesives provide a cost-effective and efficient way to bond substrates together, eliminating the need for traditional mechanical fasteners such as screws and bolts. This not only reduces manufacturing costs but also improves product performance and durability.
Benefits of Using Industrial Bonding Adhesives
Improved product performance is one of the main benefits of using industrial bonding adhesives. These adhesives can improve load-bearing capacity, stress distribution, vibration resistance, and thermal management. By providing a strong and durable bond between substrates, industrial bonding adhesives can enhance the overall performance of the product.
Enhanced product durability is another benefit of using industrial bonding adhesives. These adhesives can increase resistance to wear and tear, corrosion, moisture, and chemicals. This can extend the lifespan of the product and reduce maintenance costs.
Increased production efficiency is also a benefit of using industrial bonding adhesives. These adhesives can be applied quickly and easily, reducing assembly time and increasing production output. Additionally, they eliminate the need for additional hardware such as screws and bolts, reducing the number of parts needed for assembly.
Reduced manufacturing costs are another benefit of using industrial bonding adhesives. These adhesives are typically less expensive than traditional mechanical fasteners, reducing material costs. Additionally, they can reduce labor costs by simplifying assembly processes.
Types of Industrial Bonding Adhesives
There are several types of industrial bonding adhesives available on the market today. Each type has its own unique properties and is designed for specific applications.
Epoxy adhesives are one of the most popular types of industrial bonding adhesives. They provide a strong and durable bond that can withstand high stress and environmental conditions. Epoxy adhesives are commonly used in automotive, aerospace, and construction applications.
Acrylic adhesives are another type of industrial bonding adhesive that provides a strong bond with excellent resistance to environmental conditions such as UV light and moisture. They are commonly used in electronics and automotive applications.
Polyurethane adhesives provide a strong bond with excellent flexibility and resistance to impact and vibration. They are commonly used in construction applications.
Silicone adhesives provide a strong bond with excellent resistance to high temperatures and chemicals. They are commonly used in aerospace and electronics applications.
Cyanoacrylate adhesives provide a fast-setting bond with excellent strength and durability. They are commonly used in medical device manufacturing and electronics applications.
How Industrial Bonding Adhesives Improve Product Performance
Industrial bonding adhesives can improve product performance in several ways.
Increased load-bearing capacity is one way that industrial bonding adhesives can improve product performance. By providing a strong bond between substrates, the adhesive can distribute stress more evenly across the product, increasing its load-bearing capacity.
Improved stress distribution is another way that industrial bonding adhesives can improve product performance. By providing a strong bond between substrates, the adhesive can distribute stress more evenly across the product, reducing the risk of stress concentration points that can lead to failure.
Enhanced vibration resistance is another way that industrial bonding adhesives can improve product performance. By providing a strong bond between substrates, the adhesive can absorb vibrations more effectively, reducing the risk of damage or failure due to vibration.
Better thermal management is another way that industrial bonding adhesives can improve product performance. By providing a strong bond between substrates, the adhesive can help dissipate heat more effectively, reducing the risk of overheating or thermal damage.
How Industrial Bonding Adhesives Improve Product Durability
Industrial bonding adhesives can also improve product durability in several ways.
Increased resistance to wear and tear is one way that industrial bonding adhesives can improve product durability. By providing a strong bond between substrates, the adhesive can help prevent damage from friction or abrasion.
Improved resistance to corrosion is another way that industrial bonding adhesives can improve product durability. By providing a barrier between substrates and corrosive materials such as water or chemicals, the adhesive can help prevent corrosion from occurring.
Enhanced resistance to moisture and chemicals is another way that industrial bonding adhesives can improve product durability. By providing a barrier between substrates and moisture or chemicals, the adhesive can help prevent damage from exposure to these substances.
Best Practices for Using Industrial Bonding Adhesives
To ensure optimal performance when using industrial bonding adhesives, there are several best practices that manufacturers should follow:
Proper surface preparation is essential for ensuring a strong bond between substrates. Surfaces should be clean, dry, and free from contaminants such as oil or dust before applying adhesive.
Correct adhesive application is also important for ensuring optimal performance. Adhesive should be applied evenly across both surfaces being bonded without any air pockets or gaps.
Adequate curing time should be allowed before subjecting bonded substrates to any stress or environmental conditions. Curing times vary depending on the type of adhesive being used but should always be followed according to manufacturer instructions.
Quality control measures should be implemented throughout the manufacturing process to ensure consistent quality and performance of bonded products.
Future Trends in Industrial Bonding Adhesives and Product Development
The future looks bright for industrial bonding adhesives as new technologies emerge:
Development of new adhesive technologies will continue as manufacturers seek stronger bonds with faster curing times and improved environmental resistance properties.
Increased use of sustainable and eco-friendly adhesives will become more prevalent as manufacturers seek ways to reduce their carbon footprint while maintaining optimal performance standards.
Integration of adhesives with other manufacturing processes such as 3D printing will become more common as manufacturers seek ways to streamline production processes while maintaining optimal performance standards.
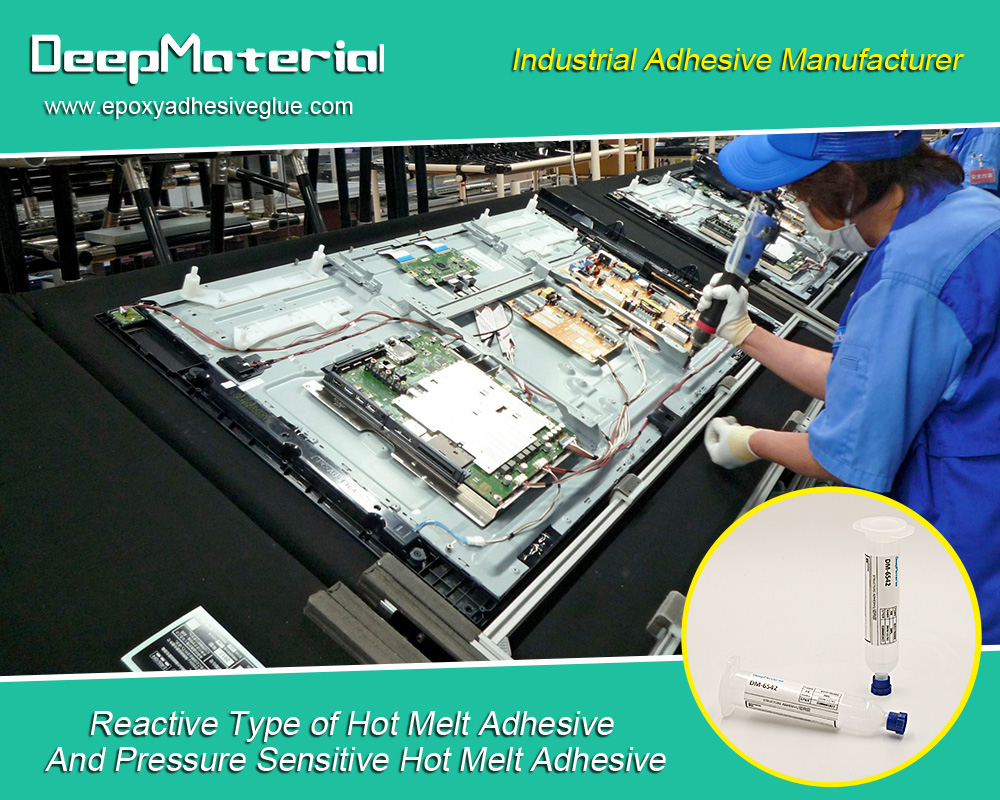
Conclusion
Industrial bonding adhesives play an important role in modern-day manufacturing processes by providing cost-effective solutions for joining substrates together while improving overall product performance and durability standards across various industries such as automotive, aerospace, electronics, construction among others. Manufacturers must consider various factors when selecting an appropriate type of industrial bonding adhesive including substrate materials; environmental conditions; curing time; strength requirements; chemical resistance among others.
For more about choosing the Industrial bonding adhesives, you can pay a visit to DeepMaterial at https://www.epoxyadhesiveglue.com/ for more info.