Hot Pressing Decorative Panel Bonding: A Comprehensive Guide
Hot Pressing Decorative Panel Bonding: A Comprehensive Guide
The aesthetic appeal of surfaces plays a crucial role in interior design and furniture manufacturing. Decorative panels, which add elegance and sophistication, are often used in various applications, from cabinetry to wall coverings. The bonding process, specifically hot pressing, is critical in manufacturing these panels. Hot pressing decorative panel bonding ensures the surface finish adheres firmly to the substrate, creating a durable and high-quality product. This article will comprehensively overview the hot pressing process, its benefits, techniques, and applications in decorative panel bonding.
What is Hot Pressing Decorative Panel Bonding?
Hot pressing decorative panel bonding refers to using heat and pressure to bond a decorative surface to a substrate, such as plywood, MDF (medium-density fiberboard), or particleboard. The primary objective of this process is to ensure that the decorative layer, which could be a veneer, laminate, or paper overlay, remains securely attached to the substrate, providing an appealing finish and enhancing the product’s durability.
The Hot Pressing Process: How It Works
The hot pressing process typically involves the application of heat and pressure to a decorative panel and its substrate, resulting in a strong, permanent bond. This method can be carried out in several stages to ensure precision and high-quality results. Below is a step-by-step breakdown of the process:
Step 1: Preparation of Substrate and Decorative Layer
- Surface Preparation:The substrate material is cleaned and treated to remove any dust, debris, or contaminants that may interfere with the bonding process.
- Adhesive Application:A layer of adhesive is applied evenly on the substrate, ensuring adequate coverage to provide a strong bond between the decorative surface and the base material.
- Placement of Decorative Surface:The decorative surface material (veneer, laminate, etc.) is positioned carefully on the adhesive-coated substrate, ready for the pressing process.
Step 2: Applying Heat and Pressure
Once the layers are aligned, the prepared panel is placed into the hot press machine. The machine applies heat and pressure simultaneously to activate the adhesive and create a tight bond between the decorative surface and the substrate.
- Temperature:The press typically operates at 120°C to 160°C, depending on the adhesive and bonded materials.
- Pressure:The pressure applied ranges between 0.8 to 1.2 MPa, sufficient to compress the materials and remove any air pockets that could weaken the bond.
- Time:The bonding process usually lasts between 3 to 15 minutes, depending on factors like material thickness, adhesive type, and the specific requirements of the application.
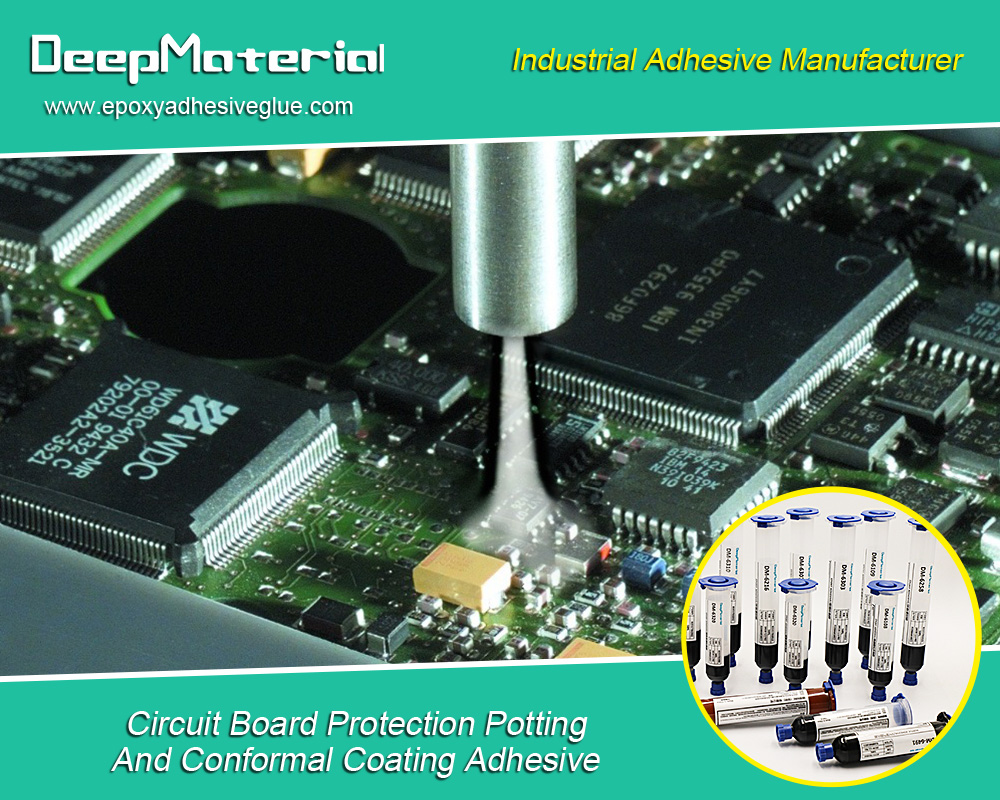
Benefits of Hot Pressing in Decorative Panel Bonding
- Superior Bond Strength
The combination of heat and pressure ensures that the adhesive is evenly distributed and fully activated, resulting in a strong and reliable bond.
it minimizes the chances of delamination, common in panels bonded using cold-press or adhesive-only methods.
- High-Quality Finish
Hot pressing ensures that the decorative surface is applied without wrinkles, bubbles, or other imperfections that could detract from the panel’s appearance.
The smooth, uniform finish enhances its aesthetic appeal, making it suitable for high-end interior applications.
- Durability and Longevity
The heat-activated adhesives used in hot pressing are designed to provide long-lasting bonds, even in challenging environments such as kitchens and bathrooms.
Decorative panels produced through hot pressing are resistant to wear, moisture, and heat, which prolongs their lifespan.
Techniques in Hot Pressing Decorative Panel Bonding
Single-Layer Hot Pressing
This method applies only one layer of decorative material to the substrate during the pressing process. It is the most common technique used for wood veneers and laminates.
- Application: Cabinetry, wall panels, and office furniture
- Advantages: Simplifies the process and reduces production time
Multi-Layer Hot Pressing
Multiple layers of decorative materials are applied for thicker or more complex panels. Each layer is bonded in succession, with hot pressing performed at each stage.
- Application: High-end furniture, architectural panels, and specialty products
- Advantages: Provides a more durable, aesthetically rich finish
Continuous Hot Pressing
This technique passes the panel through a continuous press, where heat and pressure are applied in a moving line rather than a single stationary press. This method is ideal for large-scale production.
- Application: Flooring, wall cladding, and large decorative panels
- Advantages: Increased efficiency and reduced production costs
Applications of Hot Pressing Decorative Panels
Hot pressing decorative panels are used in a wide variety of industries and settings thanks to the versatility and durability they offer. Some typical applications include:
1. Furniture Manufacturing
Hot pressing is extensively used in furniture production, especially for tabletops, cabinetry, and shelving. The process ensures that the decorative panels are aesthetically pleasing and durable enough to withstand everyday wear and tear.
Benefits in Furniture:
- Smooth and even finishes for premium appeal
- Resistance to scratches and heat
- Customization options with a variety of decorative materials
2. Interior Design
Decorative panels produced through hot pressing are often used in interior design for wall coverings, ceiling panels, and decorative partitions. The ability to apply a wide range of finishes makes hot-pressed panels a go-to choice for architects and designers.
Benefits in Interior Design:
- Wide variety of finishes, including wood, metallic, or fabric-like appearances
- Durability for high-traffic areas
- Easy maintenance
3. Automotive Interiors
Hot pressing is also used in automotive manufacturing, especially for interior components such as dashboard panels and door trims. The process ensures that decorative materials adhere correctly to the vehicle’s interior surfaces, providing aesthetic and functional benefits.
Benefits in Automotive Interiors:
- High resistance to temperature variations
- Consistent finish for a premium look
Challenges and Considerations in Hot Pressing
While hot pressing decorative panels offer many advantages, there are some challenges and considerations to keep in mind:
- Material Selection
Not all materials are suitable for hot pressing. Substrates and decorative surfaces must be compatible with heat and pressure to ensure proper bonding. Materials sensitive to high temperatures may warp or degrade during the process.
- Adhesive Compatibility
Choosing a suitable adhesive is critical for successful bonding. To provide a lasting bond, adhesives must be compatible with the substrate and decorative surface. Factors such as curing time, heat resistance, and environmental factors (humidity, temperature) must be considered.
- Cost and Energy Consumption
Hot pressing requires specialized machinery and consumes energy for heating and pressing. It can increase production costs, particularly in small-scale manufacturing operations. Energy-efficient machines and process optimization can help mitigate these costs.
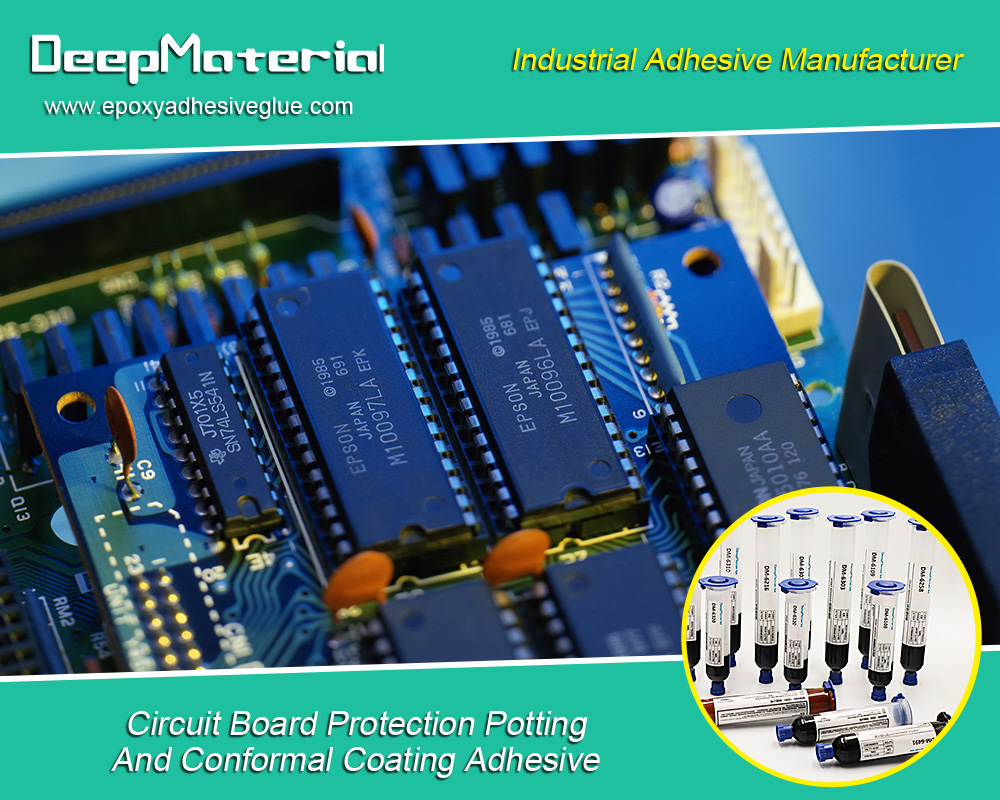
Conclusion
Hot pressing decorative panel bonding is an essential technique in modern manufacturing, offering a blend of durability, aesthetic appeal, and efficiency. From furniture and interior design to automotive and construction applications, hot-pressed panels are widely used across industries for their superior bond strength and high-quality finishes. By understanding the materials, techniques, and benefits of hot pressing, manufacturers can produce decorative panels that meet the highest quality and durability standards, ensuring long-lasting and visually appealing products.
For more about choosing the best hot pressing decorative panel bonding: a comprehensive guide, you can pay a visit to DeepMaterial at https://www.epoxyadhesiveglue.com/category/epoxy-adhesives-glue/ for more info.