Epoxy Resin Manufacturers in the USA: A Comprehensive Overview
Epoxy Resin Manufacturers in the USA: A Comprehensive Overview
Epoxy resin has emerged as a vital component across various industries due to its remarkable properties, such as high strength, durability, and resistance to environmental degradation. As the demand for epoxy resin continues to grow, particularly in sectors like construction, automotive, aerospace, electronics, and marine applications, the need for reliable and innovative manufacturers becomes more pressing. This article provides an in-depth look at the epoxy resin industry in the USA, exploring its applications, trends, manufacturing processes, and the critical factors that differentiate top manufacturers.
Understanding Epoxy Resin
Epoxy resin is a versatile polymer known for its excellent mechanical and thermal properties. It is created through a chemical reaction between epichlorohydrin and bisphenol-A (or other polyphenols), resulting in a highly cross-linked and durable structure. This structure allows epoxy resin to offer:
- High Adhesion: Epoxy resin bonds well with various substrates, including metals, wood, glass, and plastics, making it ideal for coatings and adhesives.
- Chemical Resistance:Its ability to resist chemicals and moisture makes it suitable for protective coatings and sealants.
- Mechanical Strength: Epoxy resin’s high tensile and compressive strength allows it to withstand significant stress, enhancing structural integrity in construction and automotive parts.
- Electrical Insulation: Epoxy resin is an excellent insulator, and it is widely used in electronic applications like circuit boards and transformers.
- Thermal Stability:It can endure high temperatures, making it suitable for applications that require heat resistance.
Critical Applications of Epoxy Resin
The extensive range of properties epoxy resin offers makes it suitable for various applications. Some of the key industries utilizing epoxy resin include:
- Construction: Epoxy resins are used in concrete repair, floor coatings, and protective coatings for steel structures.
- Automotive: The automotive industry uses epoxy resin to bond, seal, and manufacture lightweight composite materials that enhance fuel efficiency.
- Aerospace:Due to its lightweight and high-strength properties, epoxy resin is essential for creating composite materials for aircraft components.
- Electronics: Epoxy resin is crucial for encapsulating electronic components, providing insulation, and protecting against moisture and contaminants.
- Marine: Epoxy resin is used in boat and shipbuilding for coatings, repairs, and composite parts manufacturing.
- Art and Crafts: Artists use epoxy resin to create jewelry, sculptures, and other decorative items due to its precise, glossy finish and ease of coloring.
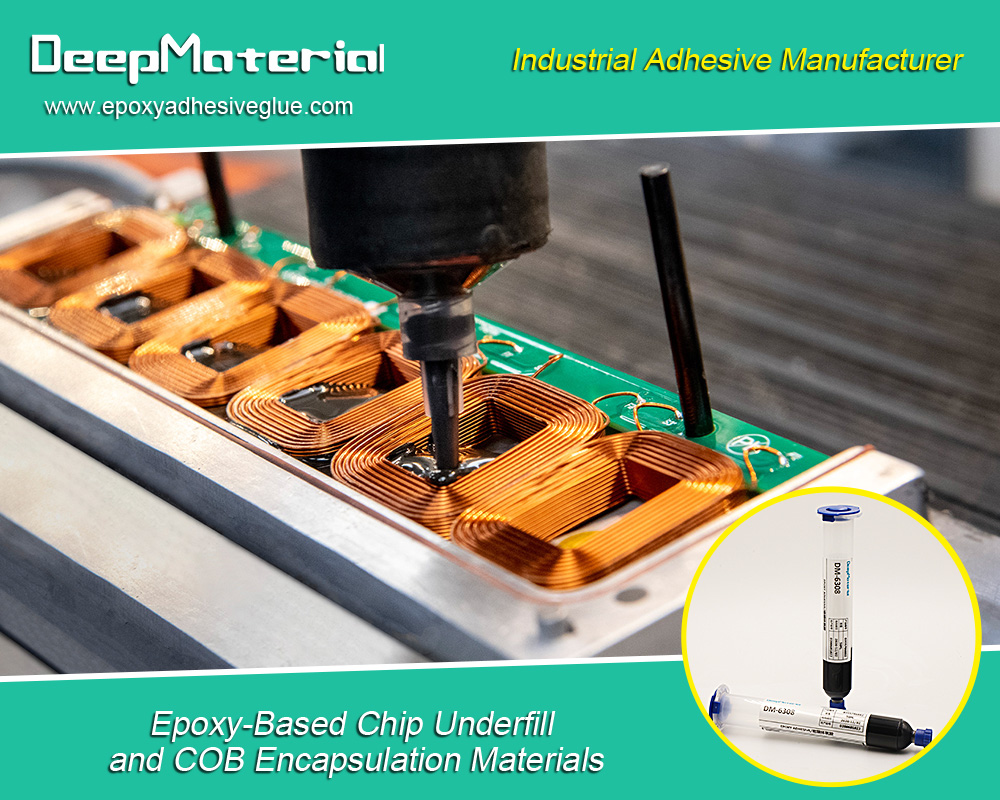
Trends in the Epoxy Resin Market
The epoxy resin industry in the USA is experiencing several notable trends that are shaping its future direction:
- Sustainability: With growing environmental concerns, manufacturers focus on developing eco-friendly epoxy resins from bio-based materials. This shift reduces dependency on petrochemicals and aligns with sustainable practices.
- Advanced Composites: The demand for lightweight and high-strength materials in the automotive and aerospace industries drives innovation in advanced epoxy resin composites, which improve performance and efficiency.
- Bright Epoxy Resins: Manufacturers are exploring brilliant epoxy resins with self-healing, conductive, and responsive properties to enhance functionality in electronic and structural applications.
- Increased Automation:Automation in manufacturing processes improves efficiency, reduces costs, and enhances the precision of epoxy resin production.
- Customization:There is a growing demand for customized epoxy resin solutions tailored to specific industrial needs, promoting innovation and customer-centric approaches.
Manufacturing Process of Epoxy Resin
The manufacturing process of epoxy resin involves several critical steps that ensure the final product meets the desired quality standards. While variations exist depending on the specific type of epoxy resin being produced, the general process includes:
- Raw Material Selection: Epoxy resin production begins with selecting the appropriate raw materials, primarily epichlorohydrin, and bisphenol-A, or alternative polyphenols for bio-based resins.
- Reaction Process: The raw materials undergo a chemical reaction, typically involving a two-step process of glycation and polymerization, to form the epoxy resin prepolymer.
- Curing Agents:The addition of curing agents, such as amines or anhydrides, initiates the cross-linking process, which solidifies the resin and enhances its properties.
- Formulation: Manufacturers may add various additives, fillers, and modifiers to enhance specific properties like color, UV resistance, and flexibility, catering to different application requirements.
- Quality Control: Stringent quality control measures are implemented throughout manufacturing to ensure the epoxy resin meets industry standards and customer specifications.
- Packaging: The final epoxy resin product is packaged in containers suitable for its intended use, whether for industrial or consumer applications.
Leading Factors Influencing Epoxy Resin Manufacturers
Several factors influence the success and reputation of epoxy resin manufacturers in the USA, distinguishing leaders in the industry from their competitors:
Innovation and Research
- Research and Development (R&D): Manufacturers investing heavily in R&D are better positioned to develop innovative solutions that cater to emerging market needs, such as bio-based resins and intelligent composites.
- Collaborations: Partnering with academic institutions and research organizations fosters innovation and accelerates the development of new technologies.
Quality and Standards
- Certification and Compliance: Adherence to industry standards, such as ISO certifications, ensures product quality and safety and builds trust with customers and partners.
- Quality Assurance:Implementing rigorous quality assurance protocols throughout production ensures consistent product performance and reliability.
Customer-Centric Approach
- Customization and Flexibility:Manufacturers offering customized solutions and flexible production capabilities can better meet diverse customer requirements and enhance satisfaction.
- Technical Support: Providing technical support and guidance to customers ensures successful product application and builds long-term relationships.
Sustainability and Environmental Responsibility
- Eco-Friendly Practices: Manufacturers committed to sustainable practices, such as using bio-based materials and reducing emissions, align with consumer preferences for environmentally friendly products.
- Waste Management:Efficient waste management practices minimize environmental impact and contribute to sustainability goals.
Market Reach and Distribution
- Global Presence: Manufacturers with a worldwide presence and robust distribution networks can tap into international markets and reach a broader customer base.
- Logistics and Supply Chain Management:Efficient logistics and supply chain management ensure timely delivery and reduce operational costs.
Cost Competitiveness
- Economies of Scale: Large-scale manufacturers can compete by optimizing production processes and reducing material costs.
- Operational Efficiency: Streamlining operations and adopting automation technologies improve efficiency and cost-effectiveness.
Challenges Faced by Epoxy Resin Manufacturers
While the epoxy resin industry in the USA is thriving, manufacturers face several challenges that require strategic solutions and adaptation:
Raw Material Costs
- Fluctuating Prices: The cost of raw materials, such as epichlorohydrin and bisphenol-A, can fluctuate due to market dynamics and geopolitical factors, affecting production costs.
- Supply Chain Disruptions: Supply chain disruptions, such as shortages or delays, can impact production schedules and increase costs.
Environmental Regulations
- Compliance Requirements: Stringent environmental regulations require manufacturers to adhere to emission standards and waste management practices, increasing operational complexity.
- Sustainability Goals: Manufacturers must balance sustainability goals with production efficiency, investing in eco-friendly practices and materials.
Competition and Market Dynamics
- Global Competition: The epoxy resin market is highly competitive, with international players vying for market share and driving innovation.
- Pricing Pressure: Intense competition can lead to pricing pressure, challenging manufacturers to maintain profitability while delivering quality products.
Technological Advancements
- Keeping Pace: Manufacturers must keep pace with technological advancements and invest in R&D to remain competitive and meet evolving customer demands.
- Adoption of Automation:Integrating automation and digital technologies into manufacturing processes requires significant investment and strategic planning.
Customer Expectations
- Demand for Customization: Customers increasingly seek customized solutions, requiring manufacturers to offer flexible production capabilities and tailored formulations.
- Quality Assurance:Meeting high customer expectations for quality and performance necessitates robust quality assurance processes and continuous improvement.
Future Outlook for Epoxy Resin Manufacturers in the USA
The future of epoxy resin manufacturers in the USA appears promising, driven by technological advancements, expanding application areas, and a focus on sustainability. Key trends shaping the future of the industry include:
Bio-Based Epoxy Resins
- Sustainable Solutions: The shift towards bio-based epoxy resins will continue to grow as manufacturers invest in developing eco-friendly alternatives to traditional petrochemical-based resins.
- Renewable Materials: Using renewable raw materials, such as plant-based oils and lignin, will reduce environmental impact and align with consumer preferences.
Advanced Composites and Nanotechnology
- High-Performance Materials: Developing advanced epoxy resin composites and nanotechnology will enhance material properties, improving strength, conductivity, and functionality.
- Lightweight Solutions: The demand for lightweight materials in the automotive and aerospace industries will drive innovation in epoxy resin composites, improving fuel efficiency and performance.
Smart Epoxy Resins
- Responsive Materials: Smart epoxy resins with self-healing, shape memory, and conductive properties will expand applications in electronics, construction, and beyond.
- Innovative Applications: Manufacturers will explore new applications for intelligent epoxy resins, enhancing product functionality and value.
Digitalization and Industry 4.0
- Automation and Efficiency: Adopting Industry 4.0 technologies, such as IoT, AI, and robotics, will streamline production processes, improve efficiency, and reduce costs.
- Data-Driven Insights: Leveraging data analytics will enable manufacturers to optimize operations, enhance quality control, and effectively meet customer demands.
Global Expansion and Collaboration
- International Markets: Manufacturers will explore international markets, expanding their global presence and tapping into new growth opportunities.
- Collaborative Innovation: Partnerships and collaborations with research institutions and industry stakeholders will drive innovation and accelerate product development.
Conclusion
Epoxy resin manufacturers in the USA are at the forefront of innovation, delivering high-quality solutions that cater to diverse industrial needs. With a focus on sustainability, advanced composites, and intelligent materials, the industry is poised for continued growth and evolution. As manufacturers navigate challenges and embrace emerging trends, they will play a pivotal role in shaping the future of epoxy resin applications across various sectors. The ongoing commitment to research, quality, and customer-centricity ensures that the epoxy resin industry in the USA remains a vital contributor to technological advancements and industrial progress.
For more about choosing the best epoxy resin manufacturers in the USA: a comprehensive overview, you can pay a visit to DeepMaterial at https://www.epoxyadhesiveglue.com/category/epoxy-adhesives-glue/ for more info.