Epoxy Conformal Coating: An Essential Guide for Electronic Assemblies
Epoxy Conformal Coating: An Essential Guide for Electronic Assemblies
It is no secret that epoxy conformal coating is a protective layer applied to electronic assemblies to shield them from harsh environmental factors such as moisture, dust, and debris. It is made up of a mixture of epoxy resins and hardeners, and is designed to conform to the contours of the components on the assembly. Furthermore, it plays a critical role in prolonging the lifespan of electronic devices and preventing failures caused by environmental factors.
In this article, we will explore the ins and outs of such coating and provide you with a comprehensive guide for using it in your electronic assemblies.
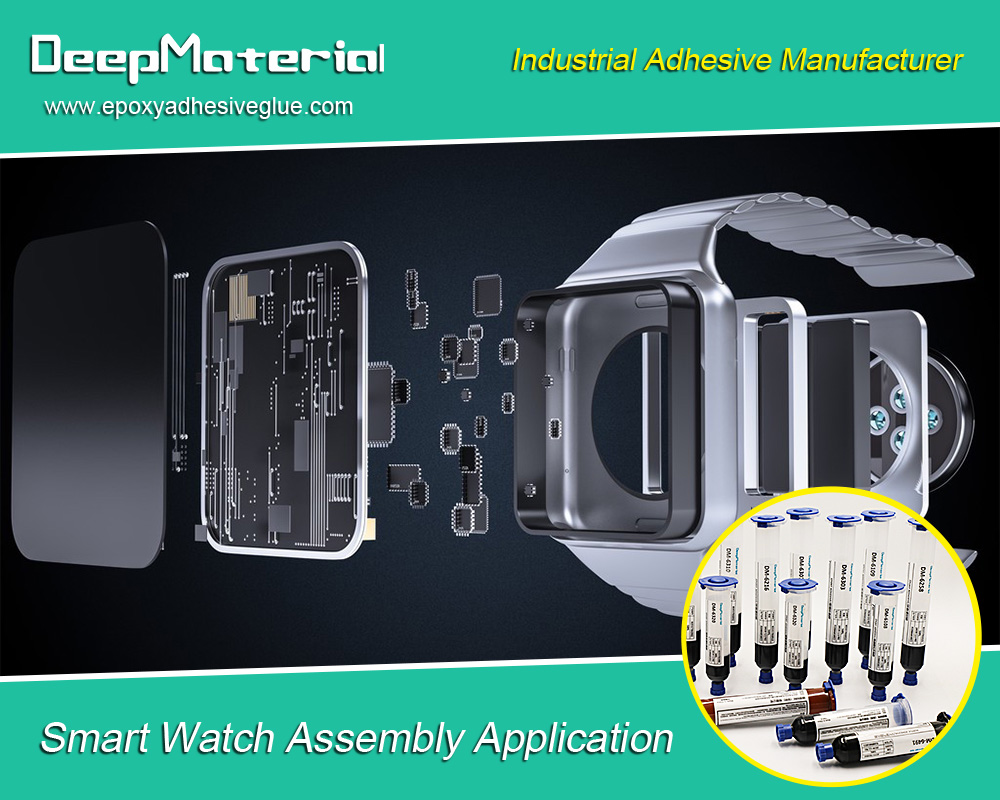
Understanding Epoxy Conformal Coating
Epoxy conformal coating is made up of a blend of epoxy resins and hardeners, which react to form a strong, protective layer. This layer adheres to the electronic assembly and conforms to the contours of the components. Such will then provide a reliable barrier against moisture, dust, and other environmental factors.
There are several types of such coating, each with its own unique properties. These include:
Standard epoxy
This type of coating provides a high level of protection against moisture and dust. Also, it has been known to be ideal for use in harsh environments.
Urethane-modified epoxy
This coating offers improved flexibility and resistance to chemicals and solvents.
Silicone-modified epoxy
This type of coating is highly flexible and offers excellent resistance to high temperatures.
Benefits of using epoxy conformal coating in electronic assemblies
These are quite numerous. They will be highlighted below:
Protection against environmental factors
It shields electronic assemblies from moisture, dust, and other environmental factors that can cause damage and failure.
Increased reliability
By protecting electronic assemblies from damage, it improves their reliability and helps to prevent costly failures.
Extended lifespan
It can extend the lifespan of electronic assemblies by preventing damage and corrosion.
Improved performance
Electronic assemblies that are protected by such coating are less likely to suffer from performance issues caused by environmental factors.
Overall, it is a critical component in the assembly and protection of electronic devices, offering numerous benefits that help to improve their reliability and extend their lifespan.
The Application Process
Proper application of such coating is essential to ensure effective protection of electronic assemblies. Here is a step-by-step guide to the application process:
Preparing the electronic assembly
- Clean the assembly thoroughly to remove any dirt, debris, or contaminants.
- Mask any areas that should not be coated, such as connectors or other sensitive components.
- Allow the assembly to dry completely before proceeding.
Applying process
- Apply the coating evenly and consistently, taking care to cover all components thoroughly.
- Use an appropriate application method, such as spraying, dipping, or brushing, depending on the size and complexity of the assembly.
- Apply multiple coats if necessary, allowing sufficient drying time between coats.
Drying and curing process
- Allow the coating to dry completely before handling or further processing the assembly.
- Cure the coating according to the manufacturer instructions, typically by exposing the assembly to heat or UV light for a specified period of time.
Common mistakes to avoid during the application
- Applying too thick or too thin of a coating which can affect the protective properties of the coating.
- Using an incorrect application method or equipment. This is capable of leading to uneven or inconsistent coverage.
- Failing to properly prepare the assembly before applying the coating. This mistake can lead to poor adhesion and other issues.
- Failing to follow the manufacturer instructions for drying and curing the coating, which can result in an inadequate protective layer.
By following these guidelines and avoiding common mistakes, you can ensure that your electronic assemblies are properly protected such coating.
Environmental Considerations for Epoxy Conformal Coating
There is no doubt that this coating is a useful and effective means of protecting electronic assemblies from environmental factors. However, it is important to consider the potential environmental impact of using and disposing of this material.
When working with it, always ensure to take the following environmental considerations into account:
Ventilation
It should be applied in a well-ventilated area to prevent exposure to harmful vapors. Ensure that the area is properly ventilated, and use a respirator if necessary.
Waste reduction
Minimize waste by carefully measuring and applying only the amount of coating needed. Avoid excess coating that may need to be disposed of later.
Disposal
It is considered a hazardous material and should be disposed of in accordance with local regulations. Do not pour unused coating down the drain. Also, and do not dispose of it with regular household waste.
Recycling
Some manufacturers offer recycling programs for used epoxy conformal coating. Check with the manufacturer to see if this is an option for you.
Safe handling and disposal of such coating is important to protect both human health and the environment. By taking these considerations into account, you can use it responsibly and minimize its impact on the environment.
Limitations of Epoxy Conformal Coating
It is a protective coating that is commonly used in electronic assemblies to protect them from harsh environmental conditions. However, like any other technology, epoxy conformal coating has its limitations. Some of the limitations of epoxy conformal coating are:
Brittle nature
These coatings are brittle in nature, which means that they can crack or break easily under mechanical stress. This can lead to the exposure of electronic components to harsh environmental conditions, ultimately leading to their failure.
Limited flexibility
They have limited flexibility and may not be suitable for electronic assemblies that require frequent flexing or bending. This can also lead to cracking or breaking of the coating.
Poor thermal conductivity
They are known to have poor thermal conductivity. This means that they can trap heat within the electronic assembly. This can lead to an increase in the operating temperature of the electronic components, ultimately leading to their failure.
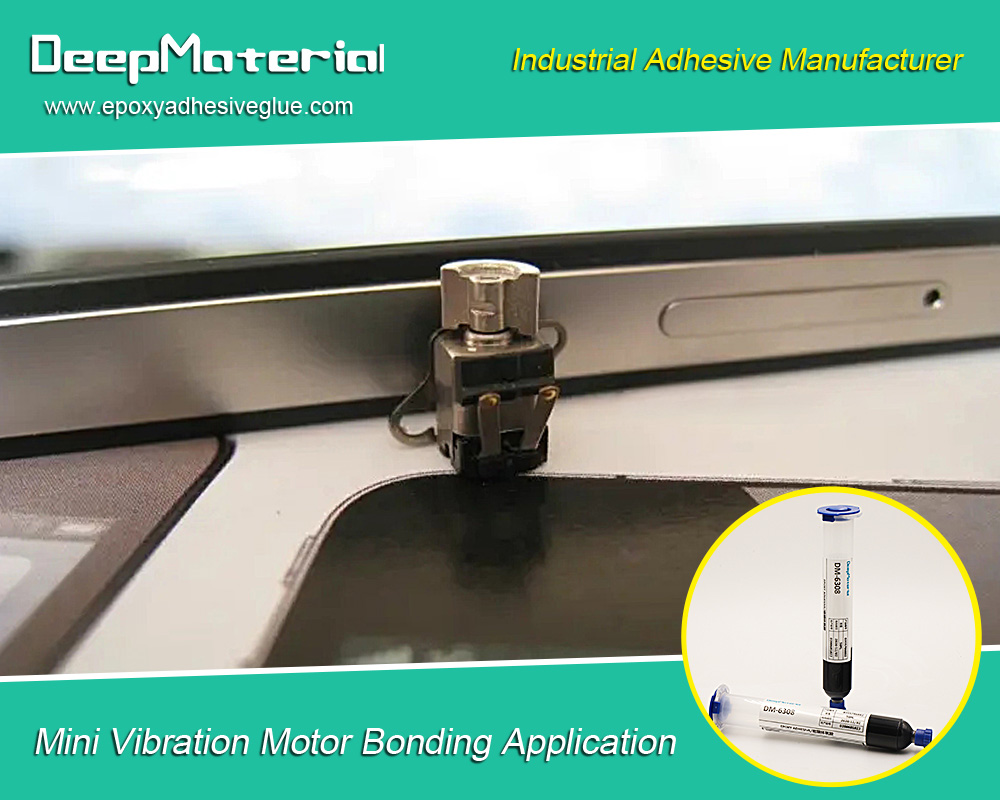
Difficult to repair
Epoxy coatings are difficult to repair once they are applied. If a component needs to be replaced or repaired, the coating has to be removed. A new coating needs to be applied, which can be a time-consuming process.
Conclusion
Having seen the above, there is every reason to believe that you are now fully equipped to make a smart decision on how to use epoxy coating. Also, you can decide whether it is a great product to use without any sentiment or bias.
For more about choosing epoxy conformal coating: an essential guide for electronic assemblies, you can pay a visit to DeepMaterial at https://www.epoxyadhesiveglue.com/category/epoxy-adhesives-glue/ for more info.