Electronic Assembly UV Curing Adhesive – Tips For Maximizing Results
Electronic Assembly UV Curing Adhesive – Tips For Maximizing Results
Are you aiming to boost the efficiency and durability of your electronic assemblies? Have you thought about the transformative impact of UV curing adhesives? In the quick-moving world of electronic manufacturing, precision and reliability are key. UV curing adhesives offer a solid solution, with fast curing times and strong bond strength. But to really make the most of their potential, it’s crucial to apply them correctly.
This article will dive into essential tips for maximizing the results of electronic assembly UV curing adhesives, making sure each application is optimized for performance and longevity. Whether you’re well-seasoned or new to the field, these insights will help you nail superior assembly outcomes.
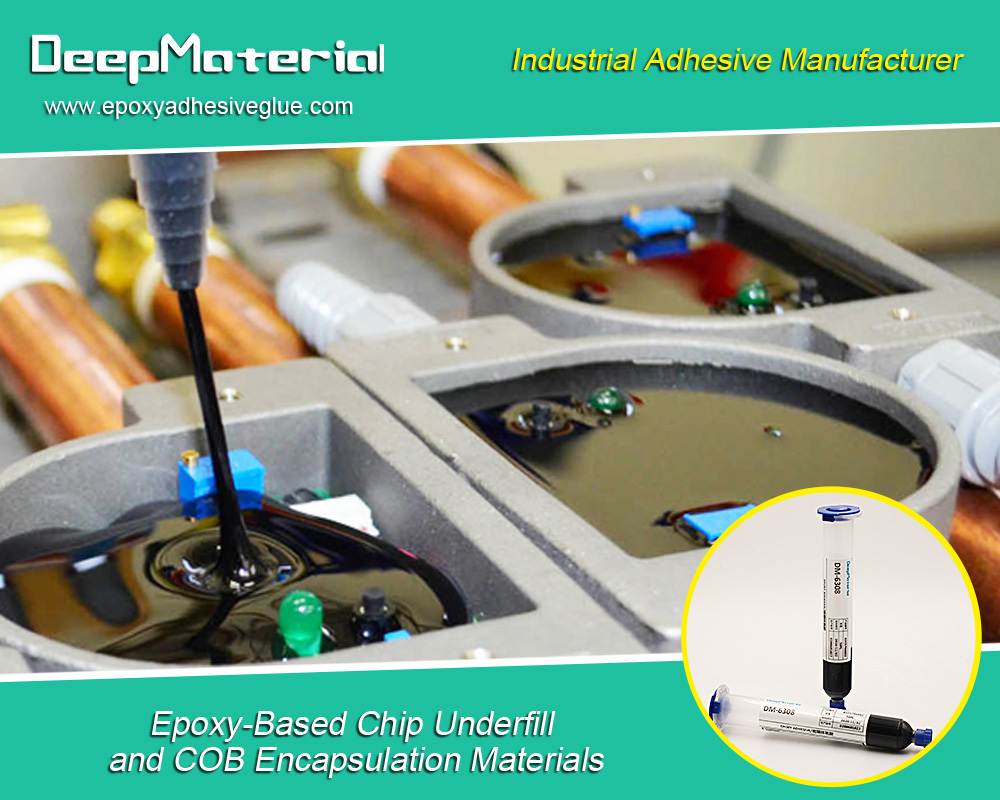
Importance of Proper Surface Preparation
Getting the surface ready is key to a successful UV curing adhesive application. Before you even think about applying the adhesive, make sure the surfaces are clean and grease-free. This step is crucial for removing any contaminants like oils, grease, or residues that might stop the adhesive from forming a strong bond.
Besides cleaning, getting the right surface roughness is vital for the best adhesion. Roughening up the surfaces, through mechanical or chemical methods, increases the area the adhesive can cling to, leading to a tougher and longer-lasting bond. This is especially important when dealing with smooth or non-porous materials often found in electronic assemblies, such as metals, plastics, or glass.
Also, keep an eye on potential contaminants and their impact on adhesion. Even tiny amounts of contaminants, such as fingerprints, dust, or leftover processing chemicals, can greatly weaken the adhesive’s ability to bond securely. Setting up thorough cleaning and inspection routines can help ensure that surfaces are spotless before applying the adhesive.
Selecting the Right UV Curing Adhesive for Your Application
Choosing the right UV curing adhesive for your electronic assembly is crucial and should be tailored to the specific needs of your application. Consider the materials and components involved, the bond strength you’re after, the operating environment, and any special performance requirements.
It’s important to evaluate the adhesive’s properties, such as viscosity, cure speed, and bond strength, to make sure it matches your needs. Adhesives with high viscosity might be better for jobs where precise placement is critical, while those with low viscosity are ideal for filling gaps. Likewise, the adhesive’s cure speed should fit with your production timeline and curing process requirements.
Material compatibility is another crucial point. Some UV curing adhesives might not play well with certain plastics, metals, or other materials in your assembly, which could lead to poor adhesion or damage to the components. Carefully checking the adhesive’s compatibility with the specific materials in your project can help ensure a strong and reliable bond.
Optimizing Adhesive Dispensing Techniques
The way UV curing adhesive is applied can seriously impact the performance and reliability of your electronic assembly. Choosing the right application method—be it bead, dot, or film—can make all the difference in getting consistent and repeatable adhesive placement.
It’s crucial to control the volume and placement of the adhesive to achieve the desired bond strength and avoid issues like using too much or too little adhesive. Getting it just right helps avoid adhesive overflow, which could mess with other components or cause contamination.
Also, making sure every application is consistent is key for maintaining quality across your assembly. Using automated or semi-automated dispensing equipment can reduce variability and ensure adhesive is applied uniformly every time.
Ensuring Adequate UV Light Exposure
The success of UV curing depends a lot on the UV light’s intensity and wavelength. It’s important to understand these factors to ensure the adhesive cures completely and reliably.
UV light intensity, measured in milliwatts per square centimeter (mW/cm²), greatly influences the curing process. Higher intensity usually means faster curing, while lower intensity might not cure the adhesive properly. Picking the right UV light source, one that fits the specific needs of your adhesive and assembly, is crucial for adequate UV exposure.
The wavelength of the UV light also matters. Different adhesives might need specific wavelengths to cure best. Making sure your UV light source matches the curing requirements of your adhesive ensures the curing is thorough and consistent across your assembly.
Monitoring Curing Time and Temperature
Getting the curing time and temperature right is vital for the adhesive’s performance and strength. Figuring out the perfect curing time for your adhesive is crucial because not enough curing can lead to weak bonding, and too much might make the adhesive brittle.
Keeping the curing temperature right is just as important because changes in temperature can affect how well and how quickly the adhesive cures. Keeping the curing within the recommended temperature range maximizes the adhesive’s effectiveness.
Continuously monitoring and adjusting the curing time and temperature during production ensures consistency and reliability in your results. Setting up real-time monitoring and feedback systems can help spot and fix any deviations from optimal curing conditions, allowing for quick adjustments and preventing potential problems.
Addressing Challenges with Shadowed Areas
In some electronic assemblies, there may be areas that are tricky to reach with UV light, creating “shadowed” regions where the adhesive doesn’t get enough exposure. Identifying these shadowed areas and figuring out how to address them is key to ensuring complete and reliable curing.
One way to tackle shadowed areas is to consider alternative curing methods or adhesive formulations that cope better with these tricky spots. For example, using a dual-cure adhesive that can be cured with both UV light and a secondary mechanism, like heat or moisture, can ensure that every nook and cranny is properly cured.
Another strategy is to tweak the design or assembly methods to reduce the impact of shadowed areas. This might mean rearranging component placement, opting for transparent or translucent materials, or adding more UV light sources to make sure every part gets enough light.
Maintaining Adhesive Storage and Handling Conditions
Keeping your UV curing adhesive in tip-top shape starts with proper storage and handling. Making sure it’s stored at the right temperature and humidity is crucial to prevent it from curing too soon or breaking down.
It’s important to stick to the manufacturer’s guidelines on shelf life and usage. Using adhesive past its expiration date can change its properties, which might mess with the bond strength and reliability.
Handling the adhesive carefully is also important to avoid contamination and premature curing. Using the right storage and dispensing gear, and maybe even UV-blocking containers or inert atmospheres, can protect the adhesive from external elements that could affect its performance.
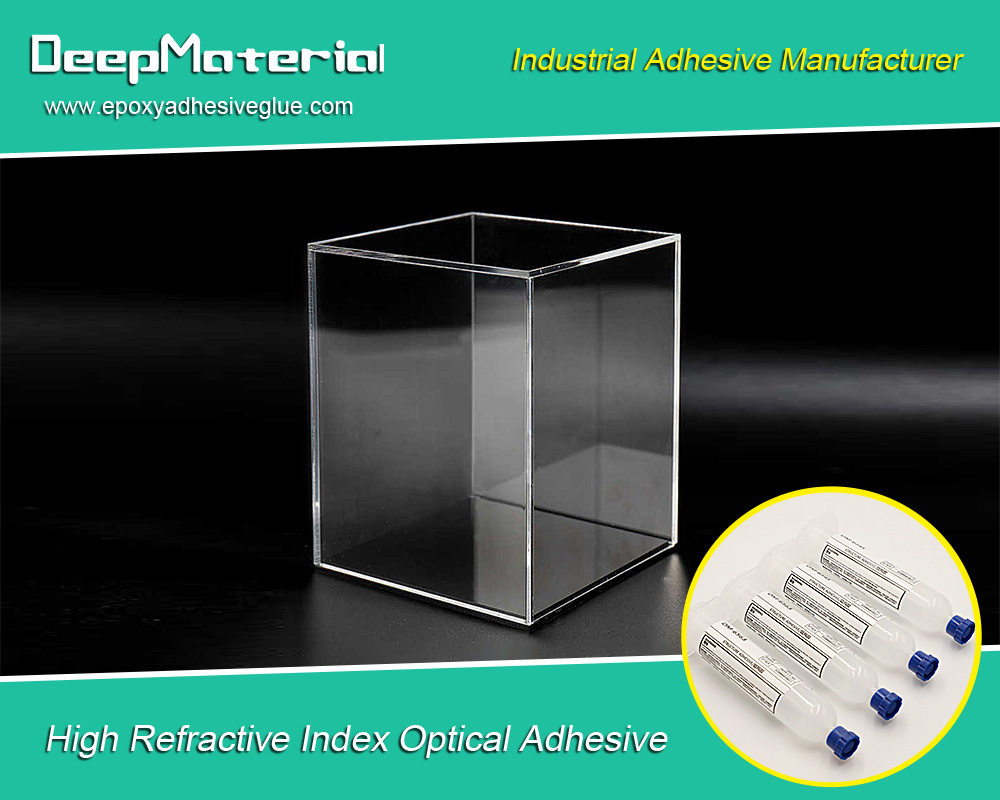
Conclusion
Even with the best planning and execution, you might run into some hiccups when using UV curing adhesives in electronic assembly. Spotting and fixing common problems is crucial for keeping the quality and reliability of the assembly up to scratch.
Issues like poor adhesion, incomplete curing, or other performance hitches can stem from various factors such as not preparing surfaces properly, using incompatible materials, or not quite right curing conditions. A systematic troubleshooting approach, like digging into the root cause and taking corrective steps, can pinpoint and fix these issues.
Improving adhesive performance might involve tweaking the surface treatment, like plasma or corona treatment, to boost the adhesive’s grip on the substrate. If the initial adhesive doesn’t meet the application’s needs, considering a different formulation might be the way to go.
Constantly striving to enhance the UV curing adhesive process is vital for maximizing the performance and reliability of your electronic assembly. This includes regular monitoring, analyzing data, and applying process improvements based on what you learn from troubleshooting and optimization activities.
By following these strategies for maximizing results with electronic assembly UV curing adhesives, you can ensure your electronic assemblies are consistently high quality, reliable, and up to the demands of your manufacturing operations.
For more about electronic assembly UV curing adhesive – tips for maximizing results, you can pay a visit to DeepMaterial at https://www.epoxyadhesiveglue.com/category/epoxy-adhesives-glue/ for more info.