BGA Package Underfill Epoxy: Enhancing Reliability in Electronics
BGA Package Underfill Epoxy: Enhancing Reliability in Electronics
In the rapidly evolving world of electronics, Ball Grid Array (BGA) packages play a crucial role in improving the performance of modern devices. BGA technology offers a compact, efficient, and reliable method of connecting chips to printed circuit boards (PCBs). However, as technology advances, so does the need for added reliability, especially in high-performance devices. It is where the BGA package underfill epoxy comes into play. This article explores the importance, application, and benefits of underfill epoxy in BGA packages and how it contributes to the longevity and performance of electronic assemblies.
What is a BGA Package?
A BGA package is surface-mount technology that attaches integrated circuits (ICs) to a PCB. Unlike traditional packages that use pins or leads for connection, BGA packages rely on an array of solder balls that form the connection between the IC and the board. These solder balls are arranged in a grid-like pattern, providing more connections in a compact space.
Advantages of BGA Packages
- Higher connection density:Compared to other package types, BGA packages offer more connections in a smaller space, making them ideal for modern, compact devices.
- Improved heat dissipation:Using many solder balls allows for better heat transfer, critical for high-performance electronics.
- Better electrical performance:BGA packages reduce the inductance and capacitance, enhancing the device’s overall electrical performance.
- Enhanced mechanical stability:Solder balls provide a more robust and reliable connection than traditional pins.
What is BGA Package Underfill Epoxy?
BGA package underfill epoxy is a specialized material applied beneath the BGA chip after soldering to enhance the mechanical stability of the connections. The primary purpose of underfill is to fill the space between the chip and the PCB, providing structural support, improving thermal cycling reliability, and protecting against mechanical stress, such as shock or vibration.
Underfill epoxy is a reinforcement for solder joints, typically susceptible to fatigue and failure due to thermal expansion mismatches between the components and the PCB. By using underfill epoxy, manufacturers can significantly enhance the reliability of electronic assemblies, particularly in demanding environments.
Critical Characteristics of Underfill Epoxy
- Low viscosity:The epoxy must flow easily to fill the gaps between the solder balls and the PCB without damaging the components.
- Cure time:Depending on the application, the epoxy may need to cure quickly or slowly, with some formulas designed for fast processing.
- Thermal conductivity:The epoxy must effectively transfer heat away from the IC to prevent overheating.
- High adhesion strength:The epoxy must bond well to the IC and the PCB to ensure mechanical stability.
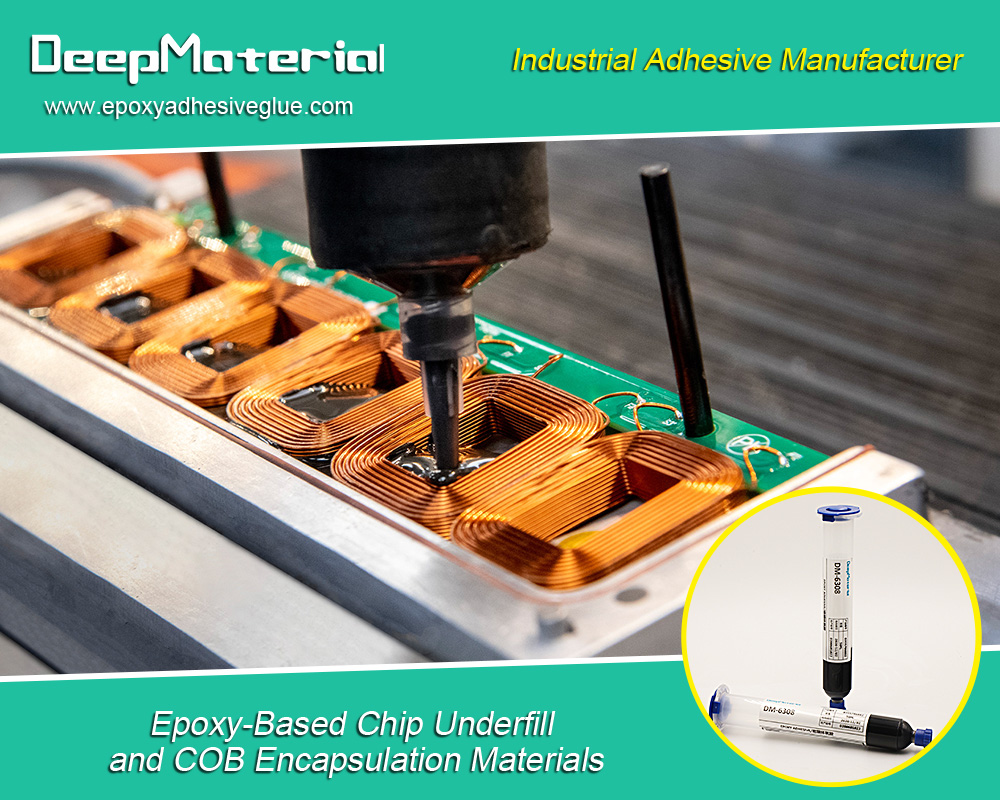
Why is Underfill Epoxy Important in BGA Packages?
As electronic devices continue to shrink in size and increase in complexity, the reliability of components such as BGA packages becomes more critical. Underfill epoxy plays a vital role in maintaining the integrity of these components by addressing several key issues:
Thermal Stress Mitigation
- Electronic components undergo constant heating and cooling cycles during operation. This thermal cycling can cause expansion and contraction of the materials, leading to mechanical stress on solder joints. Over time, these stresses can result in fatigue and eventual failure of the solder joints. By applying underfill epoxy, manufacturers can reduce the effects of thermal expansion and enhance the durability of the solder connections.
Mechanical Protection
- Devices such as smartphones, laptops, and tablets are often subjected to physical stress, such as drops, vibrations, and impacts. Solder joints in BGA packages can be vulnerable to mechanical stresses, leading to device failures. Underfill epoxy reinforces the solder joints, providing additional mechanical protection and ensuring the device functions even after experiencing physical shocks.
Improved Thermal Conductivity
- As electronic devices generate heat during operation, efficient thermal management becomes essential. Underfill epoxy helps to conduct heat away from the BGA chip and dissipate it across the PCB. This improved thermal conductivity helps to prevent overheating, which can cause malfunctions or reduce the device’s lifespan.
Enhanced Product Reliability
- Product reliability is paramount in the automotive, aerospace, and telecommunications industries. Devices used in these sectors must operate under extreme conditions without failure. By using BGA package underfill epoxy, manufacturers can ensure that their products are more reliable and less prone to failure, even under challenging environmental conditions.
Applications of BGA Package Underfill Epoxy
Consumer Electronics
- BGA package underfill epoxy is commonly used in consumer electronics such as smartphones, tablets, laptops, and wearables. These devices are designed to be compact and lightweight while offering high performance. The use of underfill epoxy helps to protect the BGA packages from mechanical stress and enhances the overall durability of the device.
Automotive Electronics
- Electronic components in the automotive industry are exposed to extreme temperatures, vibrations, and other environmental factors. Underfill epoxy ensures that BGA packages used in engine control units (ECUs), sensors, and infotainment systems remain reliable, even under harsh conditions.
Telecommunications
- Telecommunication equipment, such as routers, servers, and switches, must operate 24/7 without failure. BGA package underfill epoxy helps to ensure that the solder joints in these devices can withstand continuous thermal cycling and mechanical stress, thus maintaining uninterrupted performance.
Aerospace and Defense
- Reliability is of the utmost importance in aerospace and defense applications. BGA packages used in avionics systems, satellites, and defense equipment must withstand extreme conditions, including high vibration levels, temperature fluctuations, and radiation. Underfill epoxy provides the necessary mechanical and thermal protection to ensure the longevity of these critical components.
Benefits of Using BGA Package Underfill Epoxy
The use of underfill epoxy in BGA packages offers several advantages that contribute to electronic assemblies’ overall performance and reliability. Some of the key benefits include:
- Increased solder joint strength:Underfill epoxy reinforces the solder joints, reducing the likelihood of failure due to mechanical or thermal stress.
- Improved thermal management:The epoxy helps to dissipate heat away from the BGA chip, preventing overheating and prolonging the device’s lifespan.
- Enhanced reliability:Underfill epoxy devices are more resistant to environmental factors such as temperature fluctuations, vibrations, and physical shocks.
- Longer product lifespan:Underfill epoxy helps extend the operational life of devices by mitigating the effects of thermal cycling and mechanical stress.
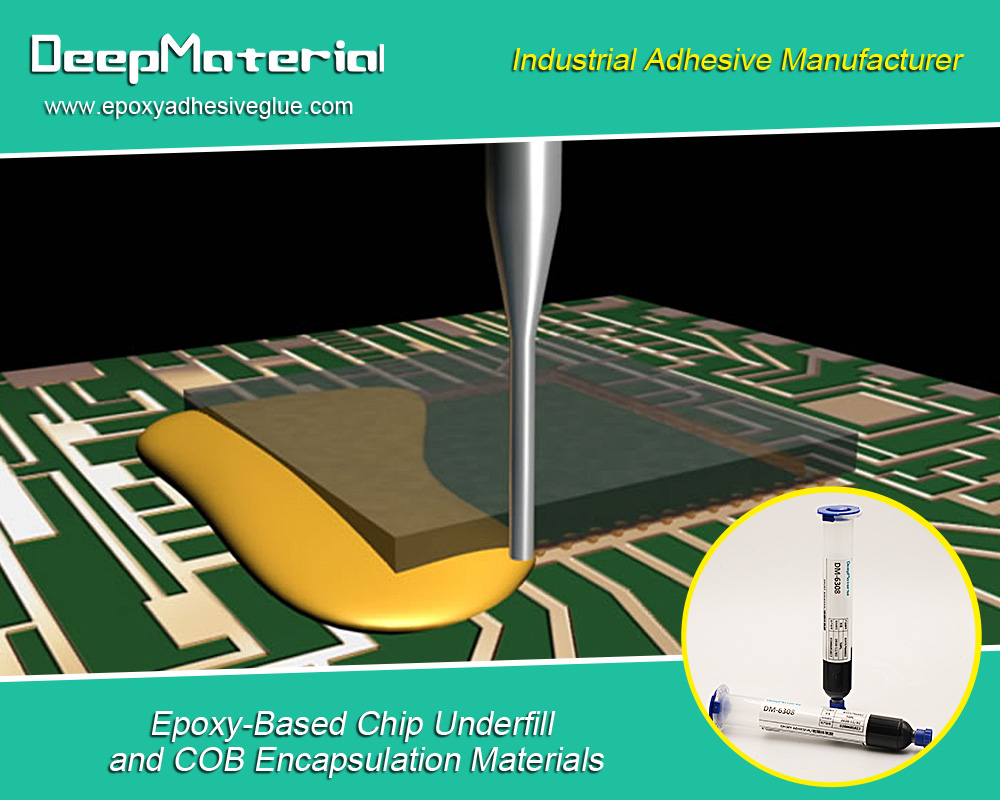
Conclusion
As electronic devices become increasingly complex and compact, the reliability of their components becomes more critical. BGA package underfill epoxy plays a vital role in enhancing BGA packages’ mechanical stability and thermal performance. From mitigating thermal stress and providing mechanical protection to improving heat dissipation, underfilling epoxy is essential in ensuring electronic assemblies’ longevity and performance. Whether in consumer electronics, automotive systems, or aerospace applications, using underfill epoxy is a crucial step in improving the overall reliability of modern technology.
For more about choosing the best BGA package underfill epoxy: enhancing reliability in electronics, you can pay a visit to DeepMaterial at https://www.epoxyadhesiveglue.com/category/epoxy-adhesives-glue/ for more info.