Benefits Of Using Structural UV-Curing Adhesives Glue In The Automobile Industry
Benefits Of Using Structural UV-Curing Adhesives Glue In The Automobile Industry
Are you aware of the transformative impact that structural UV-curing adhesives are having on the automobile industry? As car makers continually search for quicker and more dependable assembly methods, these nifty glues are grabbing the limelight. Renowned for their speedy curing times and mighty bonding power, UV-curing adhesives are changing the car-building game.
They’re speeding up production, and boosting vehicle sturdiness and safety. This article will show you how structural UV-curing adhesives are making cars not just faster to build, but also built to last.
Improved Bonding Strength and Durability
A major plus of using structural UV-curing adhesives in cars is their top-notch bonding strength and durability. These adhesives bring the muscle with superior tensile and shear strength, handling the intense stress and impacts common in cars like a champ.
Their secret? A unique curing process kicked off by UV light exposure, setting off a rapid reaction that forges a strong, cohesive bond. This not only creates a sturdy, lasting connection that handles loads and stresses well but also keeps the risk of part failures low, preserving the structural integrity of the vehicle.
Moreover, these adhesives rock at resisting thermal and mechanical stresses, perfect for the tough conditions in the automotive world. They keep their cool under extreme temperatures and vibrations, ensuring all parts stay put over the car’s lifetime. This means more reliability, fewer maintenance headaches, and longer vehicle life.
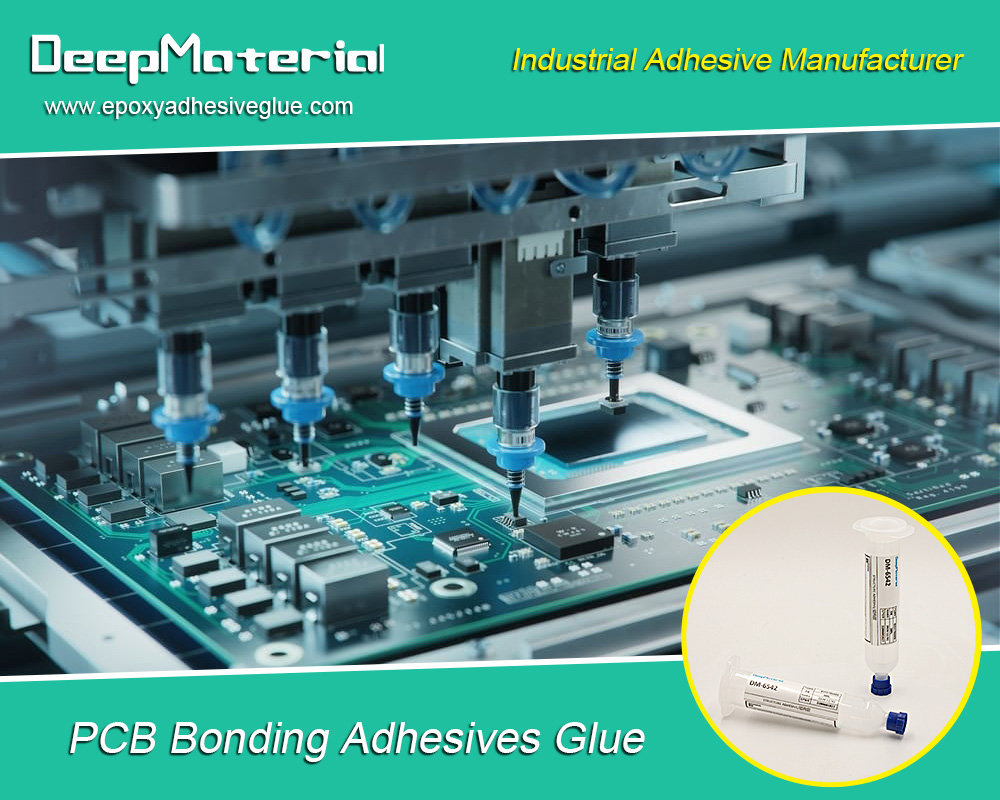
Faster Curing Times for Increased Productivity
The quick-set nature of structural UV-curing adhesives is a game-changer for car production. Unlike traditional glues that drag their heels, curing in hours or days, UV-curing adhesives get the job done in a flash once hit by UV light. This lets car makers move and assemble parts right away, slashing downtime and boosting factory flow.
This means the assembly line zips along without waiting for glues to dry. It cuts production times significantly, allowing manufacturers to crank out more cars and meet rising demands efficiently.
Plus, the fast cure times cut down on labor costs and reduce the need for fancy curing setups, making the production line more streamlined and wallet-friendly. This efficiency is a win-win, benefiting everyone from the factory floor to the consumer.
Enhanced Resistance to Environmental Factors
Car parts face all sorts of environmental threats, from moisture and chemicals to extreme temperatures. Structural UV-curing adhesives are built tough to stand up to these challenges, maintaining their bond through thick and thin.
They’re champs at blocking moisture and chemicals, creating a waterproof barrier that protects the bond from things like rain, oil, and washer fluids. This is a lifesaver for parts exposed to the rough conditions under a car or those cleaned frequently.
These adhesives also hold up well against weathering and UV rays, critical for parts exposed to the sun and varying weather conditions. This resilience ensures that cars hold their structural integrity and look good, no matter the weather.
Lightweight Design and Weight Reduction
In the car industry, shaving off pounds is a big deal because it means better fuel efficiency, zippier performance, and a smaller carbon footprint. Structural UV-curing adhesives are key players here, helping to build lighter, more efficient rides.
These adhesives are a lighter alternative to old-school methods like welding or using bolts and nuts. They’re not just featherweights themselves; they also let manufacturers apply them precisely where needed, without extra bits for support or strength.
The ripple effect of this weight loss is huge. Lighter cars need smaller engines and less power to zoom around, which means they guzzle less gas and puff out fewer pollutants. Plus, they handle better and stop quicker, which can really spice up your driving experience.
Versatility in Bonding Diverse Materials
One of the coolest things about structural UV-curing adhesives is their ability to stick all sorts of materials together. Metals, plastics, composites—you name it, these adhesives can bond it. This opens up a world of possibilities for car designers to mix and match materials that were once tough to combine.
Traditional bonding methods can’t always handle the variety of materials used in modern cars, but UV-curing adhesives take it in stride. They can join everything from metal frames to plastic trims and even fancy composite parts. This ability lets car engineers push the envelope with designs that are not only creative but also robust.
The versatility of these adhesives means designers aren’t just stuck with one material palette. They can experiment with new combinations that enhance both the car’s performance and its curb appeal. Plus, easier bonding makes the whole manufacturing process more streamlined, reducing costs and making the assembly line more efficient.
Improved Safety and Crash Performance
When it comes to cars, safety is never a laughing matter. Structural UV-curing adhesives are serious about boosting the safety and crash-worthiness of vehicles, making them safer for everyone inside.
These adhesives are super strong and durable, which means they can take a hit. During a crash, the bonds they form hold up under extreme stress, helping to keep the car’s structure intact and everyone inside safer.
Their strength is especially crucial in areas like crumple zones and safety beams. By keeping these parts solid and in place, UV-curing adhesives improve a car’s ability to absorb and dissipate crash energy, which can be a lifesaver.
Cost-Effectiveness and Reduced Manufacturing Costs
In the dog-eat-dog world of car making, cutting costs and streamlining manufacturing are key to staying ahead. Enter structural UV-curing adhesives—these handy glues are not just sticking parts together; they’re also helping save some serious coin.
Here’s the deal: these adhesives don’t need as much material as older methods like welding or using screws. That means buying less stuff to get the job done. Plus, they set super fast, so cars get put together quicker, cutting down on labor costs big time.
But wait, there’s more! Since these adhesives cure at the speed of light (UV light, that is), there’s no need to hang around waiting or splash out on special curing zones or fancy gear. This makes the assembly line faster and cheaper, which could mean lower prices for the end product—everyone loves a bargain!
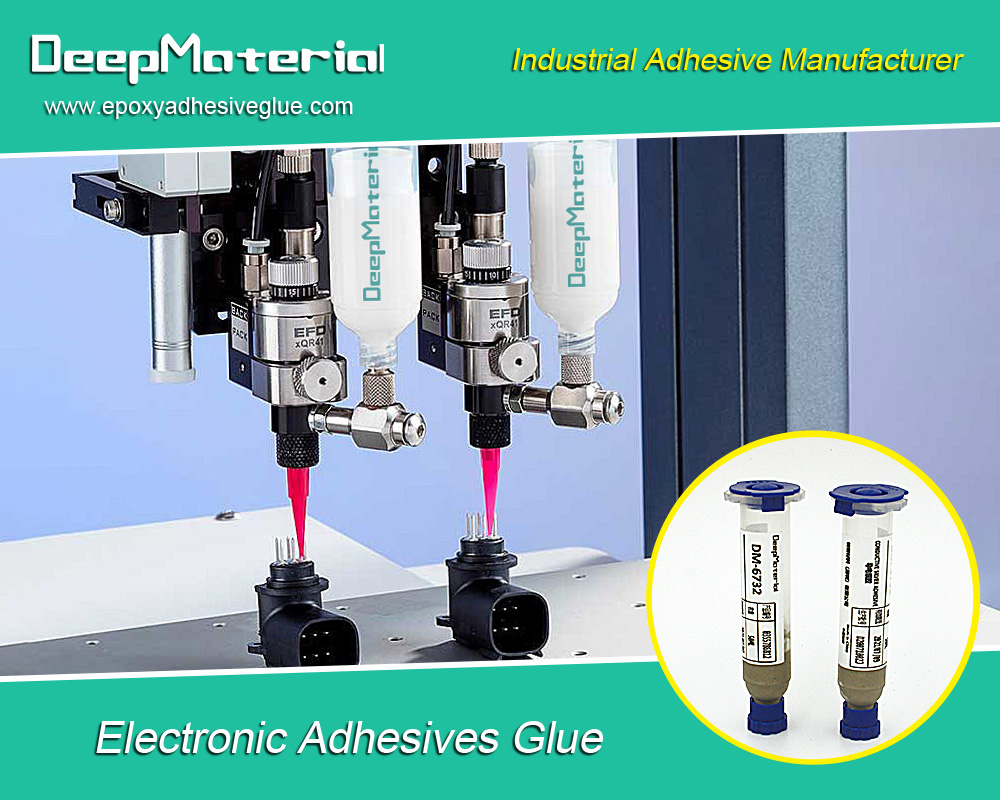
Last Words
In conclusion, the use of structural UV-curing adhesives in the automobile industry offers significant advantages, including enhanced efficiency, superior bonding strength, and increased durability. These adhesives provide a reliable solution for complex assemblies and materials, reducing production times and improving overall vehicle performance.
By enabling lighter and more innovative designs through effective bonding of dissimilar materials, UV-curing adhesives play a crucial role in advancing automotive technology and sustainability. As the industry continues to evolve towards more environmentally friendly and technologically advanced solutions, the adoption of UV-curing adhesives is likely to expand, further revolutionizing automotive manufacturing processes.
For more about choosing the benefits of using structural UV-curing adhesives glue in the automobile industry, you can pay a visit to DeepMaterial at https://www.epoxyadhesiveglue.com/category/epoxy-adhesives-glue/ for more info.