An Overview Of BGA Underfill Process And Non Conductive Via Fill
An Overview Of BGA Underfill Process And Non Conductive Via Fill
Flip chip packaging exposes chips to mechanical stress because of extensive coefficient thermal expansion mismatch between the silicon chips and the substrate. When there is a high thermal load, the mismatch stresses the chips, thus making reliability a concern. Manufacturers use single underfill layers to fill the gaps between IC chips and substrates, greatly minimizing reliability concerns when the solder joints are encapsulated.
The practice has been very helpful to manufacturers and has become a basic packaging procedure for electronic gadgets packaging. But what exactly is the underfill process?
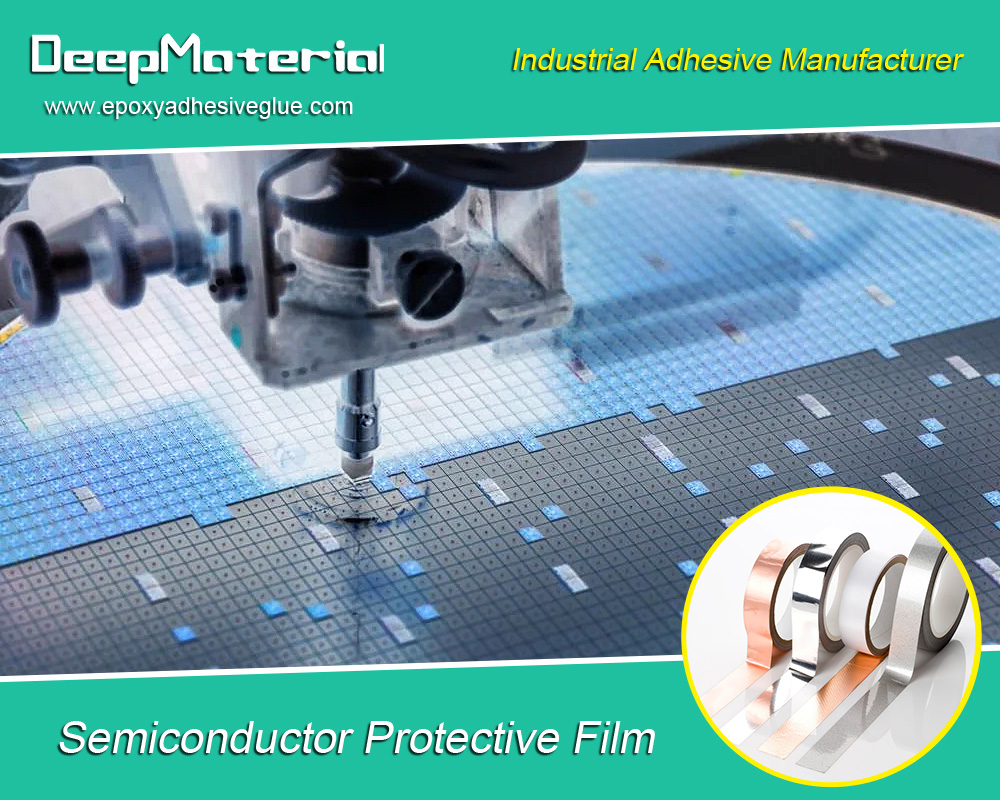
BGA underfill
An underfill can be defined as a thermoset epoxy applied to flip chips to reduce thermal stress. There are different variations of the underfill available in the market today, and manufacturers use them accordingly to boost the board-level reliability of Ball Grid Array components (BGA). The underfills are also used to boost PCB performance.
BGA underfill substances have a low mechanical and thermal load, making it possible for them to achieve their feats. As a result of low thermal and mechanical load, the substances function well even under harsh conditions providing the optimal outputs needed every time. The manufacturers get it right by considering the intended use for the underfill and its properties. Assessing how much BL reliability will be offered by the underfill is very important, and a miscalculation could be catastrophic.
The process
Ball grid array is a surface mount packaging type used by manufacturers to assemble circuit boards, mount microprocessors permanently, and permanently mount devices onto circuit boards.
BGA underfilling allows additional interconnection pins because the components make it possible to utilize the entire part at the bottom and not just the perimeter. Therefore, the interconnection pins’ net results exceed that of dual and flat inline packages. The pins are fragile and susceptible to moisture and impact damage. For this reason, manufacturers also use BGA underfill to shield circuit board assembly by boosting their mechanical and thermal properties.
In shielding PCB assembly, underfilling BGA provides a mechanical bond between the BGAs and PCBs, shielding solder joints from physical stress. The underfill also aids the efficient transfer of heat between the various BGA and PCB components.
Manufacturers use majorly epoxies as coating substances, but silicone and acrylic can also be used. The process follows the following steps:
- The underfill is applied to a chosen corner or line along the BGA
- The micro CSP or BGA is heated between 125 and 165 degrees
- Capillary action is utilized to absorb the underfill substance effectively under BGA and micro CSP
- A steady temperature is maintained for an hour to cure the underfill. The time may vary according to the used underfill component
BGA underfill applications
- BGA underfill can be applied in the following:
- Inland grid array (LGA) devices to account for chip-scale consideration and packaging density
- In chip scale packages (CSP) to prevent damages resulting from weight, shock, and vibrations.
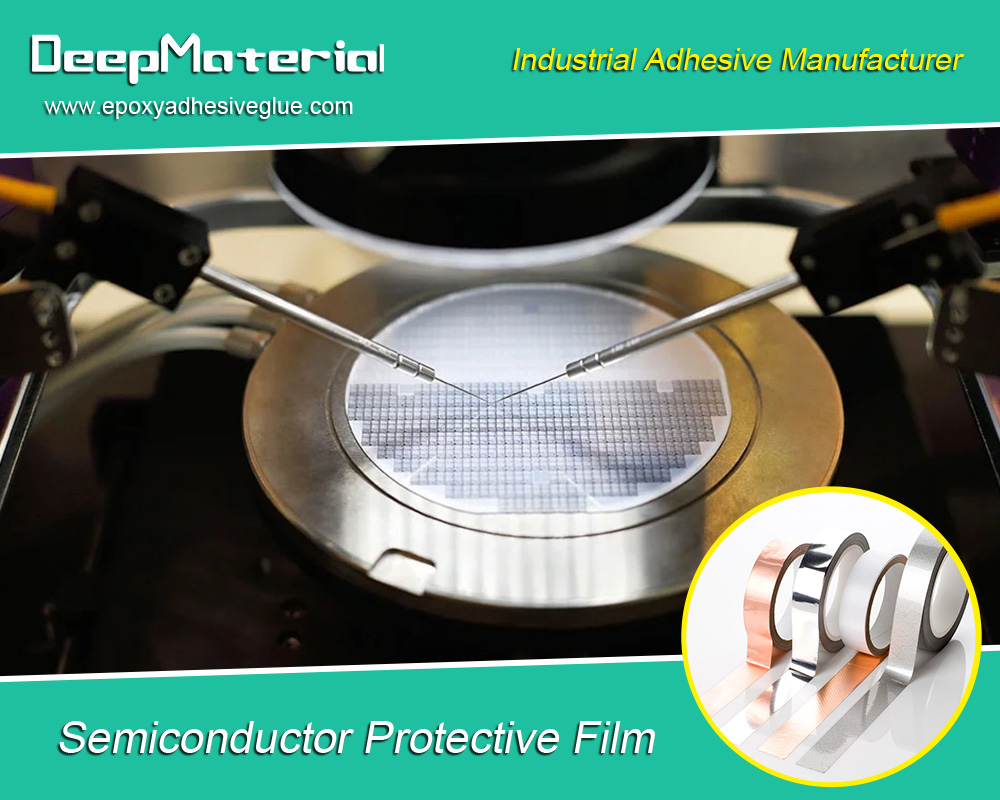
DeepMaterial offers all solutions related to underfills, bonding, and adhesives. The company manufactures high-quality products that go beyond expectations in delivering targeted results. Whatever your application needs, you can fully rely on the experts to deliver and even formulate a product that meets your exact requirements.
For more about an overview of bga underfill process and non conductive via fill,you can pay a visit to DeepMaterial at https://www.epoxyadhesiveglue.com/bga-package-underfill-epoxy/ for more info.