Acrylic vs. Silicone Conformal Coating: Which Conformal Coatings Is Right For You?
Acrylic vs. Silicone Conformal Coating: Which Conformal Coatings Is Right For You?
Acrylic and silicone conformal coatings are excellent ways to protect your electronics and other devices. But which one is right for you? The answer depends on several factors, including your device’s material, your condition, and what you hope to accomplish with the coating. In this article, we’ll go over some common questions about these two products and the best way to make that decision for yourself.
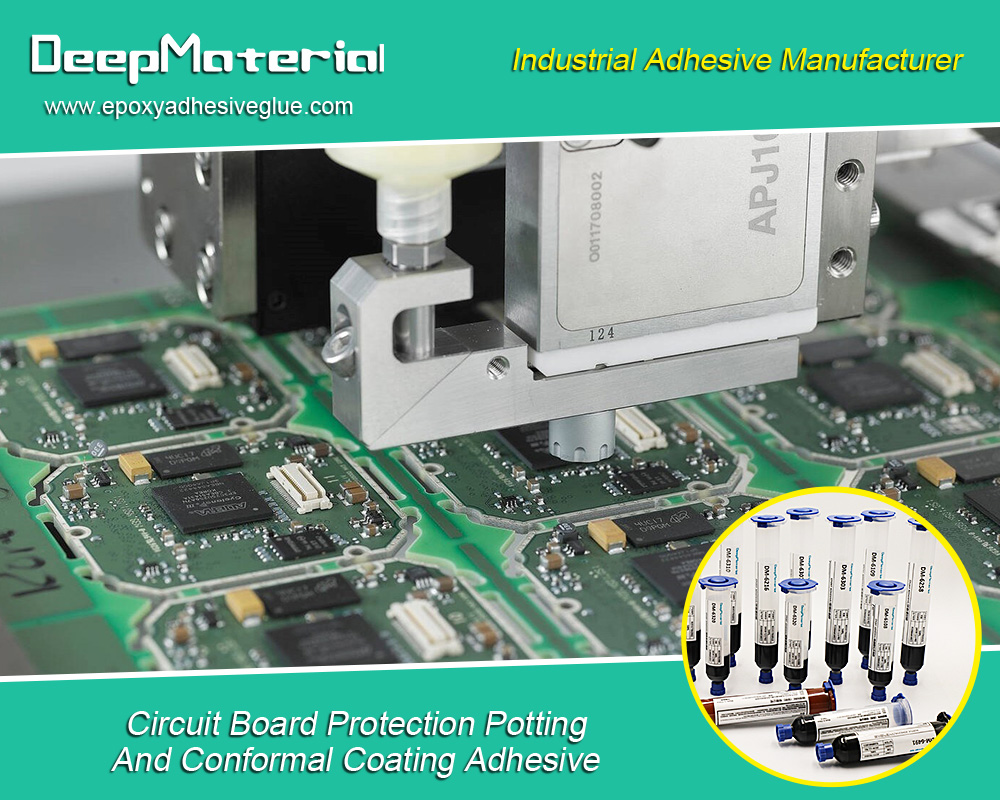
What is a Conformal Coating?
A conformal coating is a thin film applied to electronic circuitry to protect it from the environment. The primary purpose of a conformal coating is to insulate exposed metal surfaces, preventing short circuits and corrosion. Conformal coatings can be made from various materials, including acrylics, silicones, and polyurethanes. Each type of material has unique properties that make it more or less suitable for specific applications.
Acrylic conformal coatings are typically made from polymers such as polymethyl methacrylate (PMMA). PMMA is a transparent, colourless polymer with good chemical resistance and dielectric properties. Acrylics are generally easy to apply and have good adhesion to various substrates. They can be cured at low temperatures, making them ideal for sensitive electronic applications. However, acrylics are not as durable as other conformal coatings and may become yellow over time.
Silicone conformal coatings are made from silicone polymers such as polydimethylsiloxane (PDMS). PDMS is a transparent, colourless polymer with excellent chemical resistance and dielectric properties. Silicones have good adhesion to various substrates and can be cured at high temperatures. This makes them ideal for use in high-temperature applications such as automotive electronics. However, silicones are more expensive than other types of conformal coatings.
Benefits of a Conformal Coating
There are many benefits of using a conformal coating on your Printed Circuit Board (PCB), including:
- Protection from the environment: A conformal coating protects your PCB from the harsh environment it will be exposed to, including moisture, dust, chemicals and temperature extremes. This can help to prolong the lifespan of your PCB.
- Improved electrical performance: A conformal coating can improve the electrical performance of your PCB by providing a uniform dielectric layer over the surface of the board. This can help to reduce crosstalk and electromagnetic interference (EMI).
- Enhanced mechanical strength: A conformal coating can add mechanical power to your PCB, helping to protect it from physical stress and impact damage.
- Reduced manufacturing costs: Using a conformal coating can simplify the manufacturing process for your PCB, as it eliminates the need for costly manual assembly processes.
- Increased reliability: A conformal coating can improve the reliability of your PCB by protecting against environmental and electrical stressors.
How to Apply Conformal Coating
Several methods can apply a conformal coating to a PCB, including spray, dip, and brush.
- Spray coating: The most common method used to apply a conformal coating to a PCB. This method uses a spray gun to apply the coating material evenly over the board’s surface.
- Dip coating: Dip coating involves immersing the PCB in a vat of conformal coating material, allowing it to evenly coat the entire surface of the board.
- Brush coating: Brush coating involves applying the conformal coating material evenly over the board’s surface.
Pros and Cons of Acrylic vs Silicone
When choosing a conformal coating for your PCB, there are many factors to consider. Acrylic and silicone are two of the most popular choices for conformal coatings, but each has its pros and cons. Here’s a closer look at the pros and cons of acrylic vs silicone conformal coating:
Acrylic Conformal Coating:
Pros:
- Good moisture resistance
- Excellent flexibility
- Good adhesion to a variety of substrates
- Fast cure time
Cons:
- Not as durable as silicone
- Some chemicals can damage it.
Silicone Conformal Coating:
Pros:
- Excellent humidity and moisture resistance
- Good dielectric properties
- Wide operating temperature range
- Very durable
Cons:
- Slow cure time
- Limited adhesion to some substrates
How to Choose Between Acrylic and Silicone
There are many types of conformal coatings on the market, but the two most popular are acrylic and silicone. So, how do you choose between the two?
Here are some factors to consider:
- Cost: Acrylic is typically less expensive than silicone.
- Cure time: Silicone can take 24 hours or more to cure, while acrylic only takes a few hours.
- Application temperature: Silicone can be applied at lower temperatures than acrylic, so it may be a better choice if you work in a cooler environment.
- Viscosity: Acrylic is thinner than silicone, so it may be easier to apply.
- Flexibility: Silicone is more flexible than acrylic, so it’s better for applications where the coating will need to flex or move.
- Temperature resistance: Silicone can withstand higher temperatures than acrylic.
- Chemical resistance: Silicone is more resistant to chemicals than acrylic.
So, which one is right for you? It depends on your specific needs and application. If you need more clarification, ask an expert!
Considerations for Choosing Between Acrylic or Silicone
When choosing between acrylic and silicone conformal coatings, there are several factors to consider. The most crucial factor is the application and environment in which the layer will be used. Other important considerations include the following:
- The type of substrate being coated
- The desired properties of the coating
- The level of protection required.
- The cost of the coating material
Acrylic conformal coatings are typically less expensive than silicone coatings and can provide reasonable protection against moisture and dust. However, they are less durable than silicone coatings and may not provide adequate protection in more demanding environments.
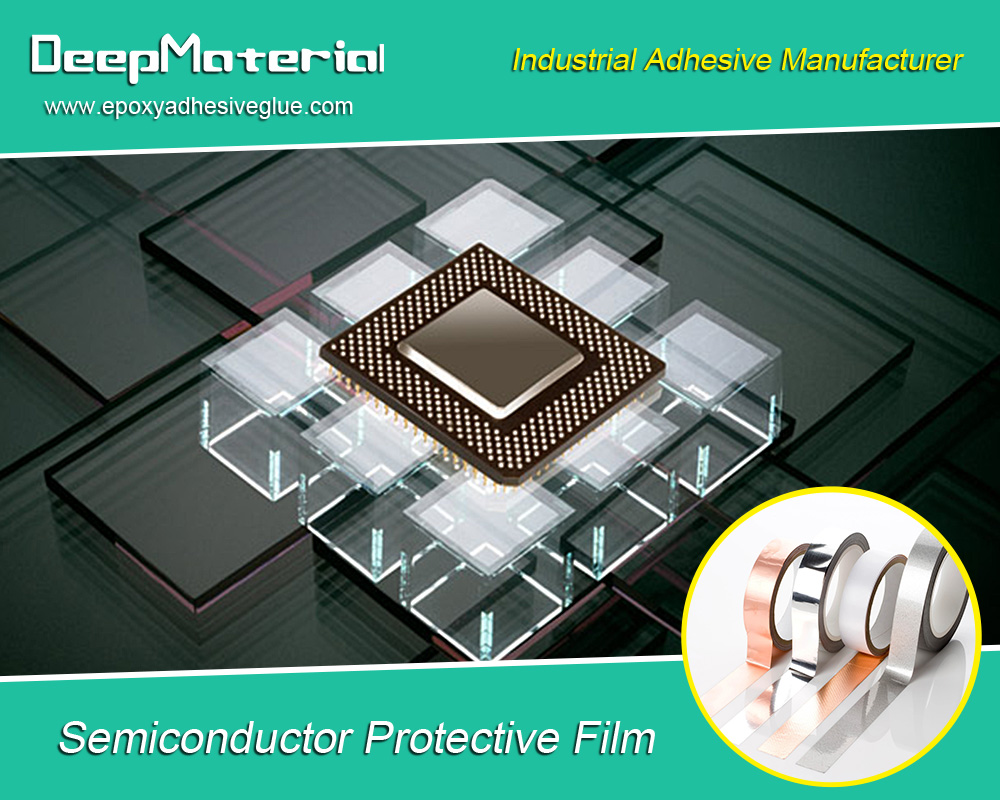
Silicone conformal coatings are more expensive than acrylics, but they are more durable and can provide better protection against chemicals and high temperatures. They are also easier to remove if repairs or modifications need to be made to the substrate.
For more about acrylic vs. silicone conformal coating: which conformal coatings is right for you,you can pay a visit to DeepMaterial at https://www.epoxyadhesiveglue.com/category/epoxy-conformal-coating/ for more info.